Composite base paper and preparation method thereof
A raw material and hexagonal technology, applied in the field of composite base paper and its preparation, can solve the problems of board appearance damage, board scrapping, etc., and achieve the effect of enhancing strength, ensuring expansion rate, and good use effect
- Summary
- Abstract
- Description
- Claims
- Application Information
AI Technical Summary
Problems solved by technology
Method used
Examples
Embodiment 1
[0018] A composite base paper, which is made of the following parts by weight of raw materials: 100 parts of softwood pulp, 780 parts of hardwood pulp, 350 parts of kaolin, 210 parts of iron yellow, 35 parts of iron red, 40 parts of magnesium saponite powder, 15 parts of ultrafine silica aerogel, 15 parts of hexagonal boron nitride powder, 8 parts of sepiolite powder, 12 parts of chestnut shell powder, 14 parts of water-based acrylic resin, 20 parts of potato starch, 3 parts of polypropylene fiber, gallic acid 5 parts of propyl ester, nano-level BaTiO 3 6 parts of powder, 8 parts of urea-formaldehyde resin.
[0019] A preparation method of composite base paper, the steps are as follows: 1. Beating: mixing softwood pulp, hardwood pulp and potato starch and then beating until the beating degree is 34°SR; 2. Adding kaolin to the beaten pulp , Magnesium saponite powder, ultrafine silica aerogel, hexagonal boron nitride powder, sepiolite powder, chestnut shell powder, propyl gallate, ...
Embodiment 2
[0021] A composite base paper, which is made of the following parts by weight of raw materials: 110 parts of softwood pulp, 815 parts of hardwood pulp, 360 parts of kaolin, 220 parts of iron yellow, 40 parts of iron red, 90 parts of magnesium saponite powder, 30 parts of superfine silica aerogel, 30 parts of hexagonal boron nitride powder, 19 parts of sepiolite powder, 18 parts of chestnut shell powder, 21 parts of water-based acrylic resin, 35 parts of potato starch, 11 parts of polypropylene fiber, gallic acid 8 parts of propyl ester, nano-level BaTiO 3 18 parts of powder, 12 parts of urea-formaldehyde resin.
[0022] A method for preparing composite base paper, the steps are: 1. Beating: mixing softwood pulp, hardwood pulp, and potato starch and then beating until the beating degree is 40°SR; 2. Adding kaolin to the beaten pulp , Magnesium saponite powder, ultrafine silica aerogel, hexagonal boron nitride powder, sepiolite powder, chestnut shell powder, propyl gallate, nano-le...
Embodiment 3
[0024] A composite base paper, which is made of the following parts by weight of raw materials: 105 parts of softwood pulp, 799 parts of hardwood pulp, 355 parts of kaolin, 212 parts of iron yellow, 37.5 parts of iron red, 56 parts of magnesium saponite powder, 22 parts of superfine silica aerogel, 24 parts of hexagonal boron nitride powder, 11 parts of sepiolite powder, 15 parts of chestnut shell powder, 18 parts of water-based acrylic resin, 22 parts of potato starch, 5 parts of polypropylene fiber, gallic acid 6 parts of propyl ester, nano-level BaTiO 3 12 parts of powder, 11 parts of urea-formaldehyde resin.
[0025] A method for preparing composite base paper, the steps are: 1. Beating: mixing softwood pulp, hardwood pulp, and potato starch and then beating until the beating degree is 36°SR; 2. Adding kaolin to the beaten pulp , Magnesium saponite powder, ultrafine silica aerogel, hexagonal boron nitride powder, sepiolite powder, chestnut shell powder, propyl gallate, nano-l...
PUM
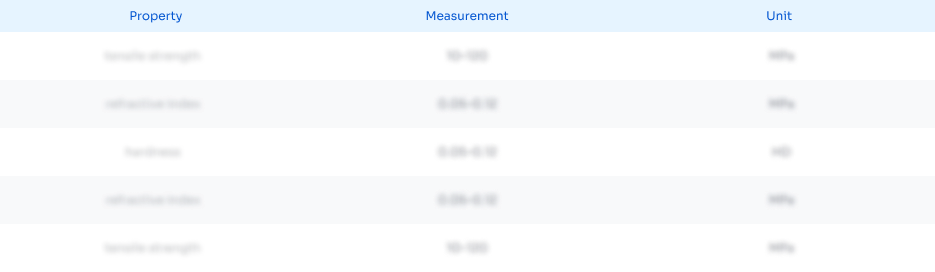
Abstract
Description
Claims
Application Information

- Generate Ideas
- Intellectual Property
- Life Sciences
- Materials
- Tech Scout
- Unparalleled Data Quality
- Higher Quality Content
- 60% Fewer Hallucinations
Browse by: Latest US Patents, China's latest patents, Technical Efficacy Thesaurus, Application Domain, Technology Topic, Popular Technical Reports.
© 2025 PatSnap. All rights reserved.Legal|Privacy policy|Modern Slavery Act Transparency Statement|Sitemap|About US| Contact US: help@patsnap.com