Method for efficiently extracting tungsten, molybdenum and copper from molybdenum slag
A molybdenum slag and high-efficiency technology, applied in the field of green extraction of non-ferrous metal smelting waste resources, can solve the problems of low added value and difficult separation of tungsten and molybdenum, and achieve the effects of high-efficiency extraction, reduced loss and solving the problem of heavy metal diffusion.
- Summary
- Abstract
- Description
- Claims
- Application Information
AI Technical Summary
Problems solved by technology
Method used
Examples
Embodiment 1
[0028] ① Leaching: Weigh 200g of dried molybdenum slag, and the slag is tested for WO 3 The Mo content is 8%, the Mo content is 25%, and the Cu content is 23%. The molybdenum slag is pretreated to remove S by hot method 2- , the burning pretreatment temperature is controlled at 573K, the pretreatment time is controlled at 3h, and the pretreatment atmosphere is controlled as an oxygen-enriched atmosphere.
[0029] ② Rod mill crushing: The pretreated molybdenum slag is crushed by a rod mill. After crushing, the particle size of the crushed material is controlled to be 92% of the mass of the material that can pass through the 325-mesh screen;
[0030] ③ Alkaline leaching of tungsten and molybdenum: add the molybdenum slag that has been milled into sodium hydroxide for leaching. The concentration of sodium hydroxide in the leaching solution is controlled at 200g / L, the leaching time is controlled at 3h, the leaching temperature is controlled at 343K, and the stirring speed is con...
Embodiment 2
[0034] ① Leaching, weighing 200g of dried molybdenum slag, the slag is tested for WO 3 Mo content is 8%, Mo content is 25%, Cu content is 23%, and molybdenum slag is pretreated to remove S 2- , the pretreatment temperature is controlled at 623K, the pretreatment time is controlled at 4h, and the pretreatment atmosphere is controlled as an oxygen-enriched atmosphere.
[0035] ② Rod mill crushing, the pretreated slag is crushed by rod mill, and the particle size of the crushed material is controlled so that the mass of the material that can pass through the 325-mesh screen accounts for 95%;
[0036] ③ Alkaline leaching of tungsten and molybdenum, the rod-milled material is added to sodium hydroxide for leaching, the concentration of sodium hydroxide in the leaching solution is controlled at 200g / L, the leaching time is controlled at 3h, the leaching temperature is controlled at 363K, and the stirring speed is controlled at 100r / min, the leaching liquid-solid ratio is controlle...
Embodiment 3
[0040] ① Leaching, weighing 200g of dried molybdenum slag, the slag is tested for WO 3 Mo content is 8%, Mo content is 25%, Cu content is 23%, and molybdenum slag is pretreated to remove S 2- , the pretreatment temperature is controlled at 673K, the pretreatment time is controlled at 3h, and the pretreatment atmosphere is controlled as an oxygen-enriched atmosphere.
[0041] ②Rod mill crushing, the pretreated slag is crushed by a rod mill, and the particle size of the crushed material is controlled so that the mass of the material that can pass through the 325 mesh screen accounts for 91%;
[0042] ③Alkaline leaching of tungsten and molybdenum, the rod-milled material is added to sodium hydroxide for leaching, the concentration of sodium hydroxide in the leaching solution is controlled at 150g / L, the leaching time is controlled at 3h, the leaching temperature is controlled at 343K, and the stirring speed is controlled at 80r / min, the leaching liquid-solid ratio is controlled...
PUM
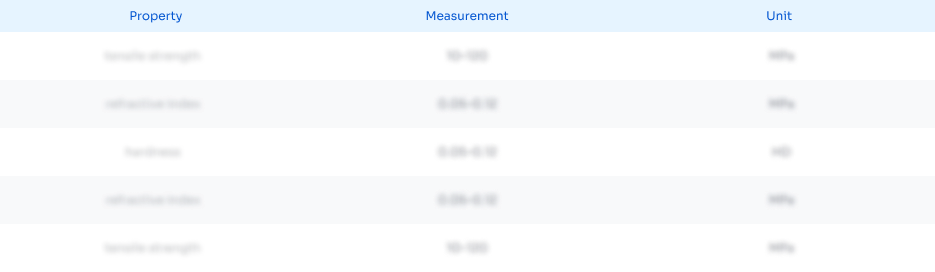
Abstract
Description
Claims
Application Information

- R&D
- Intellectual Property
- Life Sciences
- Materials
- Tech Scout
- Unparalleled Data Quality
- Higher Quality Content
- 60% Fewer Hallucinations
Browse by: Latest US Patents, China's latest patents, Technical Efficacy Thesaurus, Application Domain, Technology Topic, Popular Technical Reports.
© 2025 PatSnap. All rights reserved.Legal|Privacy policy|Modern Slavery Act Transparency Statement|Sitemap|About US| Contact US: help@patsnap.com