A kind of preparation method of sheep shearing wax all-effect effect leather
A sheep shearing and effect technology is applied in the field of preparation of sheep shearing wax effect leather, which can solve the problems of unevenness, no natural texture on the meat surface layer, no dermis layer, etc., and achieve the effect of good light resistance and color fastness.
- Summary
- Abstract
- Description
- Claims
- Application Information
AI Technical Summary
Problems solved by technology
Method used
Examples
Embodiment 1
[0026] 1) Retanning, dyeing, squeezing and stretching, stretching, scalding, and softening are performed on sheep shearing fur according to conventional techniques.
[0027] 2) Leather Grinding—Grinding with small grinding wheel 400# or 600#, there is no obvious meat residue, and the pile is uniform. Dust removal machine.
[0028] 3) Ironing shearing - spraying water on the wool surface, passing through the ironing machine at 180°C with flat rollers, and shearing machine to cut floating wool.
[0029] 4) Stretch the board according to the conventional process.
[0030] 5) Dust removal on the board surface - the compressed air pipe blows off the board dust.
[0031] 6) Spray primer - mix 90g color-changing wax WX-093, 40g resin BR-112, 40g dye water LP-4235 and 20g water (190g each) for each part to make an emulsion. Spray on the skin, about 100g / sheet, and dry at 130°C. Let it stand for 4-6 hours, and iron it with an ironing machine at 100°C, with an ironing pressure of 5-...
Embodiment 2
[0036] 1) Retanning, dyeing, squeezing and stretching, stretching, scalding, and softening are performed on sheep shearing fur according to conventional techniques.
[0037] 2) Leather Grinding—Grinding with small grinding wheel 400# or 600#, there is no obvious meat residue, and the pile is uniform. Dust removal machine.
[0038] 3) Ironing shearing - water spraying on the hair surface, 180°C flat roller ironing of the pass-through type ironing machine, and shearing machine to cut floating hair.
[0039] 4) Stretch the board according to the conventional process.
[0040] 5) Dust removal on the board surface - the compressed air pipe blows off the board dust.
[0041] 6) Spray primer - mix 100g color-changing wax WX-093, 50g resin BR-112, 50g dye water LP-4235 and 30g water (230g each) for each part to make an emulsion. Spray on the skin, about 100g / sheet, and dry at 130°C. Let it stand for 4-6 hours, and iron it with an ironing machine at 100°C, with an ironing pressure ...
Embodiment 3
[0046] 1) Retanning, dyeing, squeezing and stretching, stretching, scalding, and softening are performed on sheep shearing fur according to conventional techniques.
[0047] 2) Leather Grinding—Grinding with small grinding wheel 400# or 600#, there is no obvious meat residue, and the pile is uniform. Dust removal machine.
[0048] 3) Ironing shearing - water spraying on the hair surface, 180°C flat roller ironing of the pass-through type ironing machine, and shearing machine to cut floating hair.
[0049] 4) Stretch the board according to the conventional process.
[0050] 5) Board surface dust removal - compressed air pipe blows off board dust
[0051] 6) Spray primer - mix 110g color-changing wax WX-093, 60g resin BR-112, 60g dye water LP-4235 and 40g water (270g each) for each part to make an emulsion. Spray on the skin, about 100g / sheet, and dry at 130°C. Let it stand for 4-6 hours, and iron it with an ironing machine at 100°C, with an ironing pressure of 5-10KG / CM3. ...
PUM
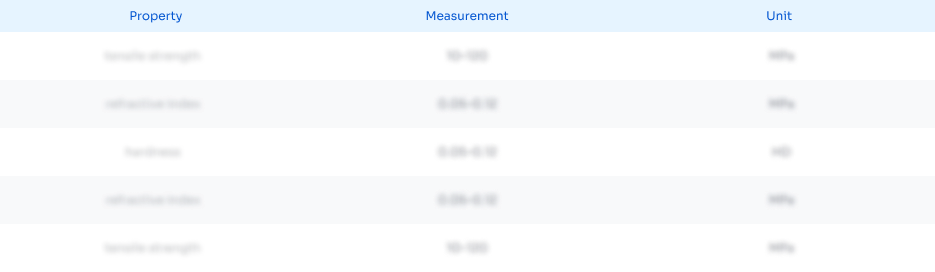
Abstract
Description
Claims
Application Information

- R&D
- Intellectual Property
- Life Sciences
- Materials
- Tech Scout
- Unparalleled Data Quality
- Higher Quality Content
- 60% Fewer Hallucinations
Browse by: Latest US Patents, China's latest patents, Technical Efficacy Thesaurus, Application Domain, Technology Topic, Popular Technical Reports.
© 2025 PatSnap. All rights reserved.Legal|Privacy policy|Modern Slavery Act Transparency Statement|Sitemap|About US| Contact US: help@patsnap.com