Robot filament winding work station
A robot and workstation technology, applied in the field of robot filament winding workstations, can solve the problems of disordered lines in the on-site control cabinet, inconvenient loading and unloading of core molds, and low production costs, achieving good axial mechanical properties, saving raw materials, and smooth and stable line shape. Effect
- Summary
- Abstract
- Description
- Claims
- Application Information
AI Technical Summary
Problems solved by technology
Method used
Image
Examples
Embodiment Construction
[0024] Attached below figure 1 The present invention is further described with specific embodiment:
[0025] A robotic fiber winding workstation, which consists of a remote control platform 1 and a fiber winding robot group 2, characterized in that the remote control platform 1 includes remote design 3, remote monitoring 5 and remote management 4, as well as a computer 25 and a switch 26 , the fiber winding robot group 2 includes at least one fiber winding robot 6 and a field control cabinet 7 of the fiber winding robot; between the remote control platform 1 and the field control cabinet 7 of the fiber winding robot, data is converted through a switch 26 and transmitted via Ethernet To transmit data; according to the needs of fiber winding, the remote control platform 1 sends control commands to the field control cabinet 7 through Ethernet, and the end effector driver 19 drives the end effector 20 with a three-jaw chuck to pick up the corresponding mandrel. Corresponding fibe...
PUM
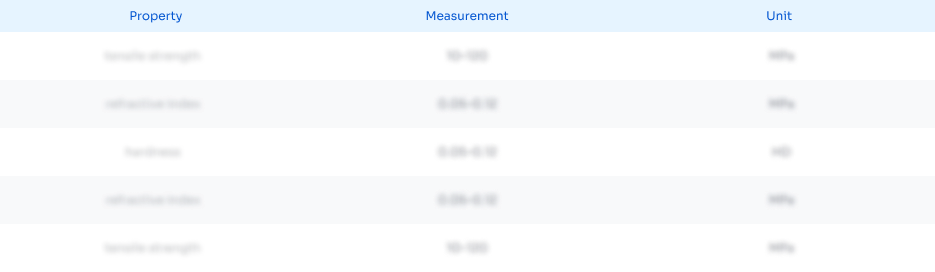
Abstract
Description
Claims
Application Information

- R&D
- Intellectual Property
- Life Sciences
- Materials
- Tech Scout
- Unparalleled Data Quality
- Higher Quality Content
- 60% Fewer Hallucinations
Browse by: Latest US Patents, China's latest patents, Technical Efficacy Thesaurus, Application Domain, Technology Topic, Popular Technical Reports.
© 2025 PatSnap. All rights reserved.Legal|Privacy policy|Modern Slavery Act Transparency Statement|Sitemap|About US| Contact US: help@patsnap.com