Automatic-casting material for coke oven coal loading holes
A coal charging hole, automatic technology, applied in coke ovens, coke oven heating, coke oven doors/closures, etc., can solve the problems of limited sealing effect, no self-flow, serious slurry settlement, etc.
- Summary
- Abstract
- Description
- Claims
- Application Information
AI Technical Summary
Problems solved by technology
Method used
Image
Examples
Embodiment 1
[0013] Adopt the material that mixes uniformly 82% pyrophyllite powder, 10% expanded vermiculite powder, 5% bentonite, 2.5% microsilica powder, 0.5% mullite fiber, add water again (relative to the weight of the material) Stir about 80% of it into a flowing slurry, and use mechanical construction methods to inject grout between the coal hole cover and the seat brick through pipes and nozzles.
Embodiment 2
[0015] Others are the same as in Example 1, but the material composition is 85% pyrophyllite powder, 8.5% expanded vermiculite powder, 2% bentonite, 4% microsilica powder, and 0.5% aluminum silicate fiber.
Embodiment 3
[0017] Others are the same as in Example 1, but the material composition is 87% pyrophyllite powder, 6% expanded vermiculite powder, 4% bentonite, 2% microsilica powder, and 1% high alumina fiber.
PUM
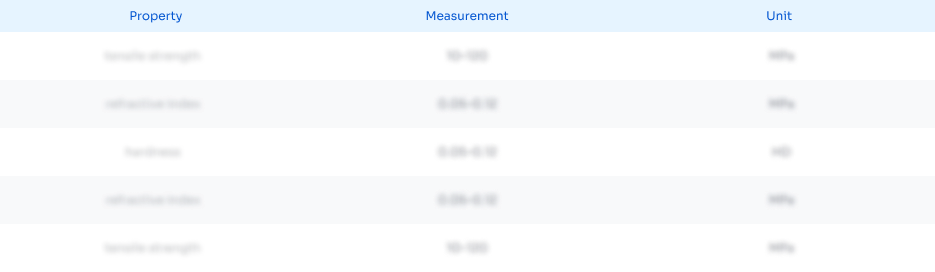
Abstract
Description
Claims
Application Information

- Generate Ideas
- Intellectual Property
- Life Sciences
- Materials
- Tech Scout
- Unparalleled Data Quality
- Higher Quality Content
- 60% Fewer Hallucinations
Browse by: Latest US Patents, China's latest patents, Technical Efficacy Thesaurus, Application Domain, Technology Topic, Popular Technical Reports.
© 2025 PatSnap. All rights reserved.Legal|Privacy policy|Modern Slavery Act Transparency Statement|Sitemap|About US| Contact US: help@patsnap.com