Coating for transformer and preparation method of coating
A technology for transformers and coatings, used in fire-resistant coatings, coatings, etc., can solve problems such as weak adhesion, easy swelling, and reduced service life of transformers, and achieves excellent sealing, compact and tight coating film, and excellent adhesion good effect
- Summary
- Abstract
- Description
- Claims
- Application Information
AI Technical Summary
Problems solved by technology
Method used
Examples
Embodiment 1
[0022] (1) Each raw material is taken by weight in the following parts: 100 parts of epoxy modified silicone resin, 25 parts of hydroxyethyl cellulose, 8 parts of talcum powder, 18 parts of ceramic microbeads, 28 parts of propylene glycol methyl ether acetate, 12 parts of nano-sized alumina, 20 parts of nano-sized magnesium oxide, 15 parts of aluminum-doped zinc oxide, 8 parts of calcium stearate, 8 parts of slag powder, 17 parts of graphite, 25 parts of xylene, 12 parts of water glass, n-butyl 12 parts of alcohol, 22 parts of filler, 11 parts of nonionic surfactant, 6 parts of curing agent, 3 parts of leveling agent, 4 parts of defoamer;
[0023] (2) Add all the raw materials into the reaction kettle, and stir at a speed of 550-650 rpm for 2-3 hours under the condition of 90-150°C;
[0024] (3) Grinding the homogeneously mixed material, and then sieving to obtain the paint, the mesh of the sieved paint is greater than 400 mesh.
Embodiment 2
[0026] (1) Take each raw material by the following parts by weight: 100 parts of epoxy-modified silicone resin, 20 parts of hydroxyethyl cellulose, 10 parts of talcum powder, 20 parts of ceramic microbeads, 32 parts of propylene glycol methyl ether acetate, 22 parts of nano-sized alumina, 28 parts of nano-sized magnesium oxide, 13 parts of aluminum-doped zinc oxide, 10 parts of calcium stearate, 9 parts of slag powder, 19 parts of graphite, 29 parts of xylene, 15 parts of water glass, n-butyl 15 parts of alcohol, 25 parts of filler, 15 parts of nonionic surfactant, 8 parts of curing agent, 5 parts of leveling agent, 5 parts of defoamer;
[0027] (2) Add all the raw materials into the reaction kettle, and stir at a speed of 550-650 rpm for 2-3 hours under the condition of 90-150°C;
[0028] (3) Grinding the homogeneously mixed material, and then sieving to obtain the paint, the mesh of the sieved paint is greater than 400 mesh.
Embodiment 3
[0030] (1) Each raw material is taken by weight in the following parts: 100 parts of epoxy-modified silicone resin, 15 parts of hydroxyethyl cellulose, 5 parts of talcum powder, 15 parts of ceramic microbeads, 26 parts of propylene glycol methyl ether acetate, 15 parts of nano-sized alumina, 25 parts of nano-sized magnesium oxide, 10 parts of aluminum-doped zinc oxide, 6 parts of calcium stearate, 6 parts of slag powder, 16 parts of graphite, 22 parts of xylene, 14 parts of water glass, n-butyl 10 parts of alcohol, 20 parts of filler, 13 parts of nonionic surfactant, 7 parts of curing agent, 2 parts of leveling agent, 4 parts of defoamer;
[0031] (2) Add all the raw materials into the reaction kettle, and stir at a speed of 550-650 rpm for 2-3 hours under the condition of 90-150°C;
[0032] (3) Grinding the homogeneously mixed material, and then sieving to obtain the paint, the mesh of the sieved paint is greater than 400 mesh.
PUM
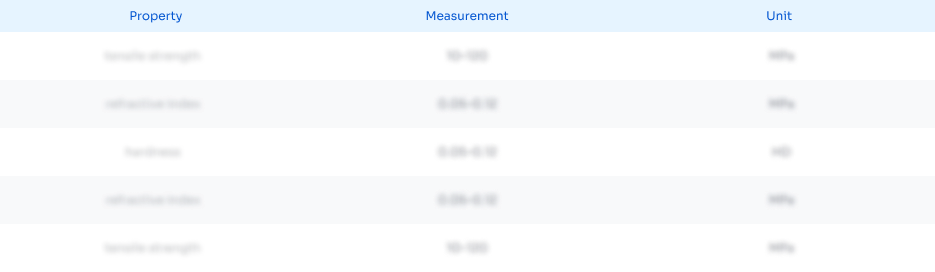
Abstract
Description
Claims
Application Information

- R&D Engineer
- R&D Manager
- IP Professional
- Industry Leading Data Capabilities
- Powerful AI technology
- Patent DNA Extraction
Browse by: Latest US Patents, China's latest patents, Technical Efficacy Thesaurus, Application Domain, Technology Topic, Popular Technical Reports.
© 2024 PatSnap. All rights reserved.Legal|Privacy policy|Modern Slavery Act Transparency Statement|Sitemap|About US| Contact US: help@patsnap.com