Method for measuring spatial orientation of pipeline based on CMOS image sensor
A technology of image sensors and measuring pipelines, which is applied in the directions of measuring devices, instruments, surveying and navigation, etc., can solve the problems that the selection of recording points is greatly affected by the environment, the accuracy of collected data is low, and the measurement accuracy is reduced, so that the applicable method is flexible, The effect of high measurement accuracy and meeting the requirements of accuracy and breadth
- Summary
- Abstract
- Description
- Claims
- Application Information
AI Technical Summary
Problems solved by technology
Method used
Image
Examples
Embodiment Construction
[0024] combine figure 1 , a method for measuring the spatial orientation of pipelines based on a CMOS image sensor. The laser beam emitted by a laser light source passes through a neutral density attenuator, passes through a bubble fluorescent ring, and is imaged on a CMOS image sensor. Through the image data acquisition and processing system, the acquired laser spot and bubble fluorescent ring images are analyzed and processed, including grayscale processing, adaptive median filtering, and the method of maximum class difference to obtain binary images, and then use the grayscale center of gravity method Calculate the pixel position of the laser spot on the photosensitive surface and the bubble position on the fluorescent ring. Use coordinate transformation to convert the pixel spot center to the actual physical spot center. When the centering device pauses every step forward, read the position of the laser spot at this position. By analogy, the positions of multiple measure...
PUM
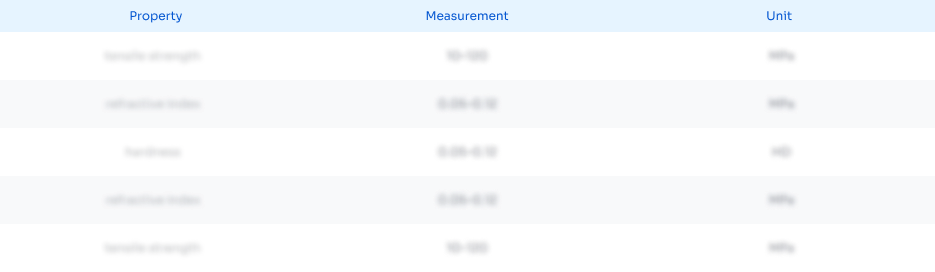
Abstract
Description
Claims
Application Information

- R&D
- Intellectual Property
- Life Sciences
- Materials
- Tech Scout
- Unparalleled Data Quality
- Higher Quality Content
- 60% Fewer Hallucinations
Browse by: Latest US Patents, China's latest patents, Technical Efficacy Thesaurus, Application Domain, Technology Topic, Popular Technical Reports.
© 2025 PatSnap. All rights reserved.Legal|Privacy policy|Modern Slavery Act Transparency Statement|Sitemap|About US| Contact US: help@patsnap.com