A machine tool cooling emulsion defoaming device and defoaming method
A defoaming device and emulsion technology, applied in the direction of foam dispersion/prevention, can solve the problems of side effects on the workpiece and human body, shorten the service life of the emulsion, and cannot be processed by machine tools, so as to reduce the cost of production and installation, simplify the structure, Good limit effect
- Summary
- Abstract
- Description
- Claims
- Application Information
AI Technical Summary
Problems solved by technology
Method used
Image
Examples
Embodiment 1
[0026] like Figure 1-3 As shown, a machine tool cooling emulsion defoaming device, which includes a liquid outlet box 1, the bottom of the liquid outlet box 1 is installed with a plurality of nuts 8 at equal intervals along its centerline position, and the liquid outlet box where the nuts 8 are located The bottom plate of 1 is machined with mounting holes, and the positions of the mounting holes are respectively installed with a first-level buffer plate 4, a second-level buffer plate 5, a third-level buffer plate 6 and a fourth-level buffer plate 7; The buffer plate is limited by the limiter 3 to open to a certain angle, and the limiter 3 is pressed and fixed on the top of the buffer plate by the locking screw 2 . During the working process, the emulsion with iron filings flows down from the top of the liquid outlet box 1, and passes through the first-level buffer plate 4, the second-level buffer plate 5, the third-level buffer plate 6 and the fourth-level buffer plate 7 in t...
Embodiment 2
[0033] A defoaming method using any machine tool cooling emulsion defoaming device includes the following steps:
[0034] Step1: Adjust the buffer angle according to the size and amount of the iron filings. When the iron filings are large, loosen the locking screw 2 and push the limiter 3 to move toward the liquid outlet. The limiter 3 drives the first-level buffer plate 4 , The second-level buffer plate 5, the third-level buffer plate 6 and the fourth-level buffer plate 7 slide in the limit groove 10, and the buffer angle becomes smaller, which is conducive to chip removal;
[0035] Step2: When the iron filings are small and few, push the limiter 3 in the opposite direction, and the buffer angle will become larger, which is conducive to defoaming. You can also adjust the buffer angles of different groups of buffer plates according to your needs to optimize the defoaming characteristics. , after the adjustment, just tighten the screw 2;
[0036] Step3: When the coolant enters...
PUM
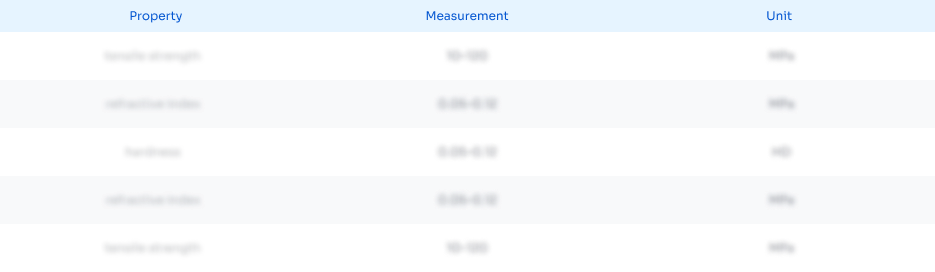
Abstract
Description
Claims
Application Information

- R&D
- Intellectual Property
- Life Sciences
- Materials
- Tech Scout
- Unparalleled Data Quality
- Higher Quality Content
- 60% Fewer Hallucinations
Browse by: Latest US Patents, China's latest patents, Technical Efficacy Thesaurus, Application Domain, Technology Topic, Popular Technical Reports.
© 2025 PatSnap. All rights reserved.Legal|Privacy policy|Modern Slavery Act Transparency Statement|Sitemap|About US| Contact US: help@patsnap.com