Preparation method of Ni-W-P graded alloy
A gradient alloy and alloy technology, applied in the field of metal protection, can solve the problems of prone to cracks, high brittleness, and high internal stress of the coating, and achieve the effect of improving corrosion resistance and wear resistance, and improving corrosion resistance and wear resistance.
- Summary
- Abstract
- Description
- Claims
- Application Information
AI Technical Summary
Problems solved by technology
Method used
Examples
Embodiment 1
[0026] Take about 800mL water and heat it to 50°C, add 80g of nickel sulfate, 20g of nickel chloride, 10g of sodium tungstate, 30g of sodium sulfate, 20g of sodium citrate, 10g of citric acid, 15g of phosphorous acid and 10g of boric acid under mechanical stirring. Set the volume to 1 L, adjust the pH value to 7 with sodium hydroxide solution, stir mechanically for 30 min, control the temperature in a constant temperature water bath to 45°C and stir for 10 min. First, the workpiece is derusted, degreased, washed, and activated in sequence according to the conventional pretreatment method, and then the pretreated workpiece is placed in the electrolyte, with the nickel plate as the auxiliary electrode and the workpiece as the working electrode. / s scanning speed from -1.3 V to -0.5 V continuously, rinse with water after plating, and dry naturally to obtain a single-layer gradient Ni-W-P alloy.
Embodiment 2
[0028] Take about 900 mL of water and heat it to 60 °C, add 20 g of nickel sulfate, 60 g of sodium tungstate, 60 g of potassium sulfate, 15 g of sodium citrate, 30 g of citric acid, 5 g of phosphorous acid, and 30 g of boric acid in sequence under magnetic stirring, and set the volume to 1 L, adjust the pH value to 6.5 with ammonia solution, stir with magnetic force for 45 minutes, control the temperature in a constant temperature water bath to 75°C and stir for 20 minutes. First, the workpiece is derusted, degreased, washed, and activated in sequence according to the conventional pretreatment method, and then the pretreated workpiece is placed in the electrolyte, with graphite as the auxiliary electrode and the workpiece as the working electrode. The scanning speed is continuously scanned from -0.5 V to -1.3 V. After plating, rinse with water and dry naturally to obtain a thinner single-layer gradient Ni-W-P alloy.
Embodiment 3
[0030] Take about 850mL of water and heat it to 55°C, add 40g of nickel sulfate, 50g of ammonium tungstate, 35g of ammonium chloride, 25g of sodium tartrate, 15g of citric acid, 10g of phosphorous acid, and 15g of boric acid under mechanical stirring, and make the volume 1 L , adjust the pH value to 7.5 with sodium hydroxide solution, stir mechanically for 20 min, and control the temperature in a constant temperature water bath to 50 °C and stir for 30 min. First, the workpiece is derusted, degreased, washed, and activated in sequence according to the conventional pretreatment method, and then the pretreated workpiece is placed in the electrolyte, with the nickel plate as the auxiliary electrode and the workpiece as the working electrode. / s scanning speed in the potential range -0.5 V - -1.3 V forward continuous scanning 10 times, rinse with water after plating, and dry naturally to obtain a single-layer gradient Ni-W-P alloy.
PUM
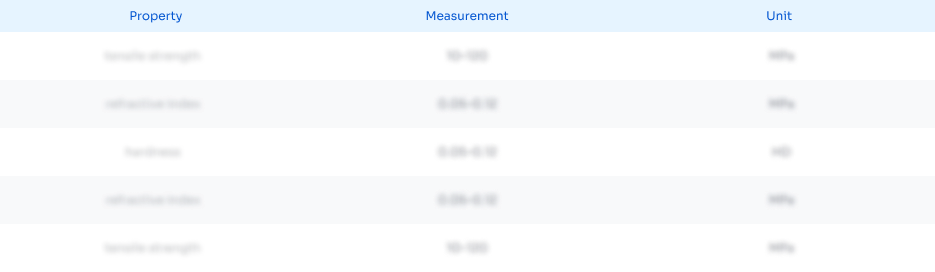
Abstract
Description
Claims
Application Information

- R&D Engineer
- R&D Manager
- IP Professional
- Industry Leading Data Capabilities
- Powerful AI technology
- Patent DNA Extraction
Browse by: Latest US Patents, China's latest patents, Technical Efficacy Thesaurus, Application Domain, Technology Topic, Popular Technical Reports.
© 2024 PatSnap. All rights reserved.Legal|Privacy policy|Modern Slavery Act Transparency Statement|Sitemap|About US| Contact US: help@patsnap.com