Cover rubber used for low-temperature vulcanized high-performance halogen-free flame-retardant laminated conveyor belt, and preparation method thereof
A low-temperature vulcanization, high-performance technology, applied in the field of conveyor belts, can solve the problems of equipment control system corrosion, loss of mechanical properties of skeleton materials, asynchronous temperature rise of rubber materials, etc. Safety, the effect of excellent mechanical properties
- Summary
- Abstract
- Description
- Claims
- Application Information
AI Technical Summary
Problems solved by technology
Method used
Image
Examples
Embodiment 1
[0024] A high-performance halogen-free flame-retardant laminated conveyor belt cover rubber, the formula ratio is as follows in parts by weight: 100 parts of rubber matrix (50 parts of EVM 400 rubber, 30 parts of EVM 500 rubber, 20 parts of EBA 17BA07 rubber), cross-linked 2.5 parts of agent (1 part of TBPO, 1.5 parts of BPO), 1.2 parts of co-crosslinking agent (1 part of TAIC, 0.2 part of HVA-2), 3 parts of plasticizer DOS, 2 parts of anti-aging agent DDA-702 parts, anti-hydrolysis agent PCD- 6 parts of 50, 2 parts of Chemmix 18D anti-sticking agent, 2 parts of silane coupling agent (1.2 parts of KH-570, 0.8 parts of SI-69), 45 parts of filling and reinforcing agent (15 parts of N234, 10 parts of N330, high dispersion SiO 2 20 parts) and 35 parts of flame retardant (15 parts of aluminum diethylphosphinate, 15 parts of diphenyl sulfone polyphenylphosphate, 5 parts of melamine polyphosphate).
[0025] Specific steps are as follows:
[0026] (1) Primary mixing: Control the te...
Embodiment 2
[0030] A high-performance covering rubber for halogen-free flame-retardant laminated conveyor belts, the formula ratio is as follows in parts by weight: 100 parts of rubber matrix (30 parts of EVM 400 rubber, 40 parts of EVM 500 rubber, 30 parts of EBA 17BA04 rubber), cross-linked 3.5 parts of agent (2 parts of TBPO, 0.5 parts of BPO, 1 part of TBPB), 2.5 parts of co-crosslinking agent (1.5 parts of TAIC, 0.5 parts of HVA-2, 0.5 parts of TMPTMA), 3 parts of plasticizer DOS, anti-aging agent DDA- 70 2 parts, anti-hydrolysis agent PCD-50 6 parts, anti-adhesive additive Chemmix 18D 2 parts, silane coupling agent 2.5 parts (KH-570 1 part, KH-550 1.5 parts), filling reinforcing agent 60 parts (N234 20 parts, highly dispersed SiO 2 40 parts), 45 parts of flame retardant (18 parts of aluminum diethylphosphinate, 15 parts of diphenyl sulfone polyphenylphosphate, 8 parts of melamine polyphosphate, 4 parts of zinc borate).
[0031] Specific steps are as follows:
[0032] (1) Primary ...
Embodiment 3
[0036] A high-performance halogen-free flame-retardant laminated conveyor belt cover rubber, the formula ratio is as follows in parts by weight: 100 parts of rubber matrix (30 parts of EVM 500 rubber, 50 parts of EVM 600 rubber, 20 parts of EBA 17BA07 rubber), cross-linked 5 parts of agent (TBPO 2 parts, TBPB 1.5 parts, CH 335 1.5 parts), co-crosslinking agent 3.5 parts (TAIC 1.7 parts, HVA-2 0.8 parts, TMPTMA 1 part), plasticizer DOS 3 parts, antioxidant DDA 2 parts of -70, 6 parts of anti-hydrolysis agent PCD-50, 2 parts of anti-sticking additive Chemmix 18D, 4 parts of silane coupling agent (2 parts of KH-570, 0.8 parts of KH-550, 1.2 parts of SI-69), filling 75 parts of reinforcing agent (25 parts of N234, 10 parts of N3302, 40 parts of highly dispersed SiO2), 60 parts of flame retardant (35 parts of polyphenylsulfone diphenyl phosphate, 12 parts of melamine polyphosphate, 13 parts of zinc borate).
[0037] Specific steps are as follows:
[0038] (1) Primary mixing: contr...
PUM
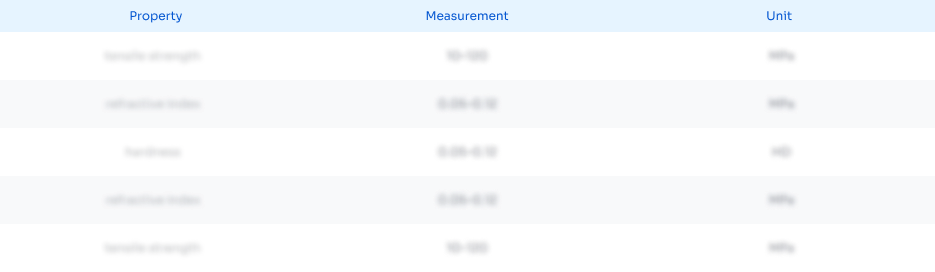
Abstract
Description
Claims
Application Information

- R&D
- Intellectual Property
- Life Sciences
- Materials
- Tech Scout
- Unparalleled Data Quality
- Higher Quality Content
- 60% Fewer Hallucinations
Browse by: Latest US Patents, China's latest patents, Technical Efficacy Thesaurus, Application Domain, Technology Topic, Popular Technical Reports.
© 2025 PatSnap. All rights reserved.Legal|Privacy policy|Modern Slavery Act Transparency Statement|Sitemap|About US| Contact US: help@patsnap.com