MgO-CaO-Fe2O3 series electric furnace ramming material prepared from fine magnesia-calcium brick powder
A technology of mgo-cao-fe2o3, magnesia-calcium bricks, applied in the field of refractory materials, can solve problems such as environmental pollution, cracks, and high energy consumption, achieve improved thermal shock stability and corrosion resistance, simple preparation process, and realize waste The effect of using
- Summary
- Abstract
- Description
- Claims
- Application Information
AI Technical Summary
Problems solved by technology
Method used
Image
Examples
Embodiment Construction
[0019] The specific implementation of the present invention will be further described below:
[0020] A MgO-CaO-Fe prepared by using fine powder of magnesium-calcium brick 2 O 3 The electric furnace ramming material is prepared from the following parts by weight: 0~0.078mm magnesia-calcium brick fine powder less than 95 parts, 0~0.078mm light burnt magnesia powder less than 50 parts, iron red less than 6 parts, MgO 1~3 parts of micropowder, α-Al 2 O 3 1 to 5 parts of micro powder, 0.5 to 5 parts of ceramic fiber, 1 to 1.5 parts of titanium oxide.
[0021] The main components in the ceramic fiber include alumina, zirconia and lanthanum oxide, and the weight ratio of the three is alumina: zirconia: lanthanum oxide=10-15:3-5:1-2.
[0022] The particle size of the MgO powder is 3-5μm, and the α-Al 2 O 3 The particle size of the micropowder is 1-3 μm.
[0023] The chemical indicators of magnesia-calcium brick fine powder and light burnt magnesia powder are shown in Table 1:
[0024] Table 1...
PUM
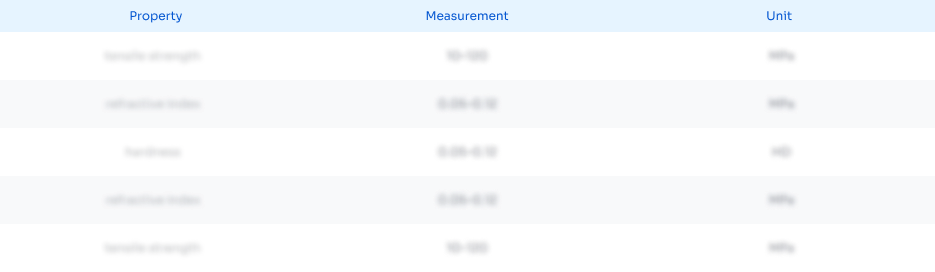
Abstract
Description
Claims
Application Information

- R&D
- Intellectual Property
- Life Sciences
- Materials
- Tech Scout
- Unparalleled Data Quality
- Higher Quality Content
- 60% Fewer Hallucinations
Browse by: Latest US Patents, China's latest patents, Technical Efficacy Thesaurus, Application Domain, Technology Topic, Popular Technical Reports.
© 2025 PatSnap. All rights reserved.Legal|Privacy policy|Modern Slavery Act Transparency Statement|Sitemap|About US| Contact US: help@patsnap.com