A Heavy Duty Fiber Molded Pallet
A molding and fiber technology, which is applied in the field of fiber molding products, can solve the problems of difficult molding of complex thick-walled structures, large deformation, large volume, etc., and achieves easy molding process realization, material saving, and structure simple effect
- Summary
- Abstract
- Description
- Claims
- Application Information
AI Technical Summary
Problems solved by technology
Method used
Image
Examples
Embodiment 1
[0047] Example 1: Selection of 4 hole types for panel concave holes
[0048] The lower surface of the panel adopts five types of panel concave hole 4 forms: regular triangle, parallelogram, rectangle, regular hexagon and circle. In order to make the trays with 5 different panel concave hole 4 structures on the lower surface of the panel comparable, all The panel concave holes 4 are arranged in a quantity of 24×20, and the volume of the control panel is the same. The width of the beams between the faces is equal everywhere (except the round holes) to ensure that the panel beams can be evenly stressed.
[0049] The geometric model is established in ProE, and then imported into ANSYS software for static structural simulation analysis. The heavy-duty fiber molding material made from waste cardboard has an elastic modulus of 3 415.3 MPa and a Poisson's ratio of 0.1. The multi-segment linear line segment combination of the multi-segment linear plastic model in ANSYS is used to app...
Embodiment 2
[0054] Example 2: Optimization of the size of the structural unit of the panel concave hole
[0055] For panels with different hole types, the maximum stress point appears at the top of the panel concave hole 4 when the load is uniform. According to the theory of material mechanics, it is mainly due to the bending moment that the maximum stress appears on the top of the panel concave hole 4, which in turn leads to panel damage. For this, take Figure 4Taking the regular hexagonal panel concave hole unit as an example, apply reverse surface pressure to the 6 outer surfaces of the panel concave hole unit, and fix the bottom surface so that each surface forms a linearly distributed bending moment for simulation analysis. The size of the panel concave hole unit mainly includes the face depth, wall thickness, draft angle and rounding radius. According to the pre-experiment, 3 levels are taken for each factor, and the orthogonal test is carried out, as shown in Table 2.
[0056] T...
Embodiment 3
[0060] Embodiment 3: Optimization of the size of the structural unit of the outrigger
[0061] In ANSYS software, the Figure 5 A surface pressure of 0.0001MPa is applied to the upper surface of the outrigger structural unit, and the bottom of the outrigger is fixed for simulation analysis. The dimensions of the outrigger structural unit mainly include thickness, draft angle, and fillet radius. According to the pre-experiment, take 3 levels for each factor and conduct an orthogonal test, see Table 3.
[0062] Table 3 Orthogonal test scheme and result analysis
[0063]
[0064]
[0065] Table 4 shows the analysis of variance of the results of the orthogonal test of the outrigger structural unit.
[0066] Table 4 variance analysis table
[0067]
[0068] From the results of variance analysis in Table 4, it can be seen that the draft angle has a highly significant effect on the maximum stress, while the thickness and round radius have no significant effect. The prim...
PUM
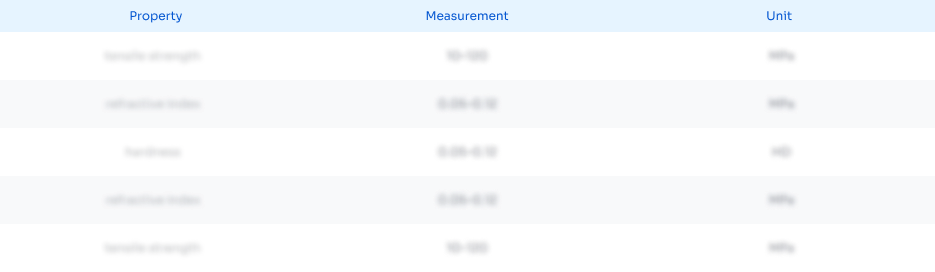
Abstract
Description
Claims
Application Information

- R&D
- Intellectual Property
- Life Sciences
- Materials
- Tech Scout
- Unparalleled Data Quality
- Higher Quality Content
- 60% Fewer Hallucinations
Browse by: Latest US Patents, China's latest patents, Technical Efficacy Thesaurus, Application Domain, Technology Topic, Popular Technical Reports.
© 2025 PatSnap. All rights reserved.Legal|Privacy policy|Modern Slavery Act Transparency Statement|Sitemap|About US| Contact US: help@patsnap.com