Waterborne alkyd resin modified by epoxy resin and organic silicon and its preparation method
A water-based alkyd resin and epoxy resin technology, used in coatings, fire-retardant coatings, polyester coatings, etc., can solve problems such as unfavorable practical use, surface dryness and slow dryness, and achieve easy construction, full paint film, and improved performance. Effects on storage stability
- Summary
- Abstract
- Description
- Claims
- Application Information
AI Technical Summary
Problems solved by technology
Method used
Image
Examples
Embodiment 1
[0034] a. Alcoholysis: Add 43.5g soybean oil, 43.5g tung oil, 3.8g pentaerythritol and 50.3g trimethylolpropane to the reaction kettle successively under the protection of nitrogen, and heat up from room temperature to 160°C, add 0.032g alcoholysis catalyst lithium hydroxide to the reactor, then heat up to 220°C at a heating rate of 60°C / h for alcoholysis reaction, when the mass concentration is 87% ethanol solution tolerance reaches 1: 4 o'clock to start cooling;
[0035] b. Esterification: When the temperature of the reactor in step a drops to 180°C, add 16.2g epoxy resin E-44, 14.8g benzoic acid, 59.7g isophthalic acid, 10.5g isophthalic acid-5- Sodium sulfonate and 0.08g of esterification catalyst dibutyltin dilaurate, install a water separator to remove the water generated by the esterification reaction at the same time, continuously feed nitrogen into the reaction kettle during the reaction, keep it at 180°C for 1 hour, and then 15°C / h heating rate to 225°C, when the ac...
Embodiment 2
[0039] a. Alcoholysis: Add 50.4g soybean oil, 50.4g tung oil, 4.4g pentaerythritol and 47.7g trimethylolpropane to the reactor successively under the protection of nitrogen. After mixing, the temperature is raised from room temperature to 160°C, add 0.036g alcoholysis catalyst lithium hydroxide to the reactor, then heat up to 220°C at a heating rate of 50°C / h for alcoholysis reaction, when the mass concentration is 87% ethanol solution tolerance reaches 1: 4 o'clock to start cooling;
[0040]b. Esterification: When the temperature of the reactor in step a drops to 180°C, add 12.3g of epoxy resin E-20, 11.8g of benzoic acid, 57.1g of isophthalic acid, and 10.8g of isophthalic acid into the reactor. Formic acid-5-sodium sulfonate and 0.08g of esterification catalyst dibutyltin dilaurate, install a water separator to remove the water generated by the esterification reaction, and continuously feed nitrogen into the reaction kettle during the reaction, and keep it warm at 180°C Af...
Embodiment 3
[0046] a. Alcoholysis: Add 54g soybean oil, 54g tung oil, 8.8g pentaerythritol and 40.4g trimethylolpropane to the reaction kettle in turn under the protection of nitrogen. After mixing, the temperature is raised from room temperature to 160°C at a heating rate of 110°C / h , add 0.042g alcoholysis catalyst lithium hydroxide to the reaction kettle, then heat up to 220°C at a heating rate of 60°C / h for alcoholysis reaction, when the tolerance of the ethanol solution with a mass concentration of 87% reaches 1:4 start to cool down;
[0047] b. Esterification: When the temperature of the reactor in step a drops to 180°C, add 10.6g of epoxy resin E-12, 11.2g of benzoic acid, 53.5g of isophthalic acid, and 11g of isophthalic acid into the reactor -5-sodium sulfonate and 0.08g of esterification catalyst dibutyltin dilaurate, install a water separator to remove the water generated by the esterification reaction, and continuously feed nitrogen into the reaction kettle during the reaction...
PUM
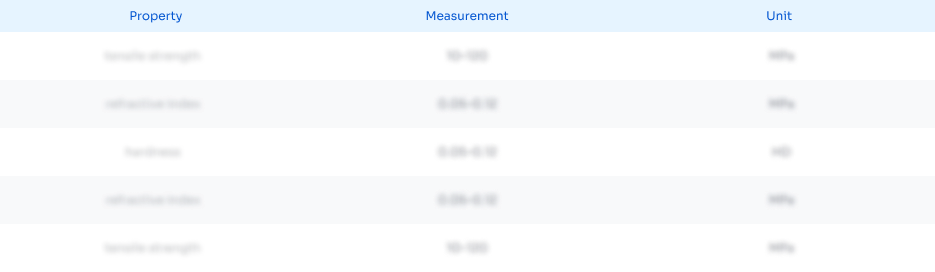
Abstract
Description
Claims
Application Information

- R&D
- Intellectual Property
- Life Sciences
- Materials
- Tech Scout
- Unparalleled Data Quality
- Higher Quality Content
- 60% Fewer Hallucinations
Browse by: Latest US Patents, China's latest patents, Technical Efficacy Thesaurus, Application Domain, Technology Topic, Popular Technical Reports.
© 2025 PatSnap. All rights reserved.Legal|Privacy policy|Modern Slavery Act Transparency Statement|Sitemap|About US| Contact US: help@patsnap.com