Working method of high-precision rubber block grabbing robot
A working method and robot technology, applied in the direction of manipulators, manufacturing tools, program-controlled manipulators, etc., can solve problems that affect the robot's grasping work, reduce the service life of the robot, and have no cooling measures, so as to achieve a good cooling effect and reduce the labor volume of personnel. Small, the effect of eliminating dust impurities
- Summary
- Abstract
- Description
- Claims
- Application Information
AI Technical Summary
Problems solved by technology
Method used
Image
Examples
Embodiment 1
[0030] Such as figure 1 As shown, the working method of a high-precision rubber block grabbing robot in this embodiment, the specific working steps are as follows:
[0031] (1), first start the power supply, and the staff sets the specific operating parameters of the robot through the PLC controller 11;
[0032] (2) The first joint axis 2 and the second joint axis 3 are driven by the servo motor inside the fuselage 1 to move to the predetermined position according to the PLC control program;
[0033] (3) The cylinder 5 drives the telescopic sleeve 6 to move downward;
[0034] (4) The telescopic sleeve 6 drives the V-shaped clamping mechanism 9 to move downward through the connecting rod 7, and at the same time, the visual inspection mechanism 14 recognizes the outline of the rubber block, judges the exact position of the rubber block and sends it to the PLC controller 11;
[0035] (5) According to the feedback information of the visual detection mechanism 14, after the V-sha...
PUM
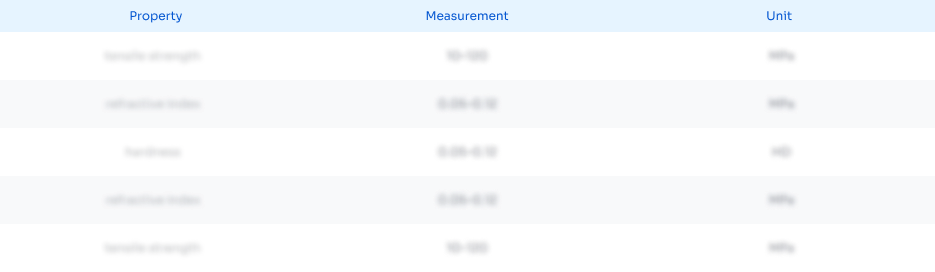
Abstract
Description
Claims
Application Information

- Generate Ideas
- Intellectual Property
- Life Sciences
- Materials
- Tech Scout
- Unparalleled Data Quality
- Higher Quality Content
- 60% Fewer Hallucinations
Browse by: Latest US Patents, China's latest patents, Technical Efficacy Thesaurus, Application Domain, Technology Topic, Popular Technical Reports.
© 2025 PatSnap. All rights reserved.Legal|Privacy policy|Modern Slavery Act Transparency Statement|Sitemap|About US| Contact US: help@patsnap.com