Damp and hot tail gas treatment process and system
A tail gas treatment and heat pump system technology, applied in heat pumps, lighting and heating equipment, combined devices, etc., can solve problems such as increased production costs, limited heat exchange efficiency, and violent molecular motion, and achieve the effects of reduced flow rate and volume reduction
- Summary
- Abstract
- Description
- Claims
- Application Information
AI Technical Summary
Problems solved by technology
Method used
Image
Examples
Embodiment Construction
[0032] Embodiments of the present invention will be further described below in conjunction with the accompanying drawings.
[0033] The wet heat tail gas treatment process of the present invention can be used for the treatment of dryer tail gas, and of course it can also be used for the treatment of high-temperature and high-humidity tail gas discharged from other equipment. Embodiment 1 of the wet heat tail gas treatment process of the present invention takes the tail gas discharged from semi-coke drying as an example, as figure 1As shown, the hot and humid tail gas 10 discharged from the dryer 1 is subjected to primary dust removal through the dust removal device 2, which can filter the large particle dust in the tail gas and is collected by the dust collection device 3; In the heat-absorbing unit 41 of the heat-pump system 4, the heat-pump system 4 absorbs the heat of the hot and humid tail gas passing through the heat-absorbing unit 41 through the electric power work unit ...
PUM
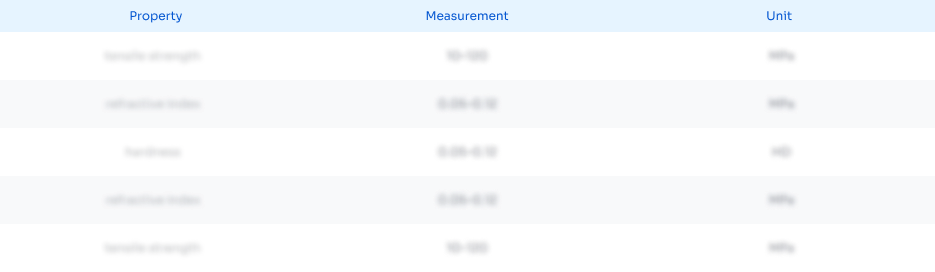
Abstract
Description
Claims
Application Information

- R&D Engineer
- R&D Manager
- IP Professional
- Industry Leading Data Capabilities
- Powerful AI technology
- Patent DNA Extraction
Browse by: Latest US Patents, China's latest patents, Technical Efficacy Thesaurus, Application Domain, Technology Topic, Popular Technical Reports.
© 2024 PatSnap. All rights reserved.Legal|Privacy policy|Modern Slavery Act Transparency Statement|Sitemap|About US| Contact US: help@patsnap.com