Gear pump and method for manufacturing same
A technology of gear pumps and internal teeth, applied to pumps, pump components, rotary piston pumps, etc., can solve problems such as volumetric efficiency reduction, noise, vibration, etc.
- Summary
- Abstract
- Description
- Claims
- Application Information
AI Technical Summary
Problems solved by technology
Method used
Image
Examples
Embodiment Construction
[0015] Next, modes for implementing the present invention will be described with reference to the drawings.
[0016] figure 1 It is a schematic configuration diagram showing the gear pump 1 according to one embodiment of the present invention. The gear pump 1 shown in this figure is configured, for example, as an oil pump mounted on a vehicle not shown, which sucks hydraulic fluid (ATF) stored in an oil pan and pressurizes it to a hydraulic control device (both not shown). deliver. The gear pump 1 includes, for example: a pump housing (both not shown in the drawing) composed of a pump body fixed to a transmission housing of an automatic transmission and a pump cover fastened to the pump body; and an inner rotor (transmission gear) 2 and an outer rotor (driven gear) 3, the inner rotor (transmission gear) 2 and the outer rotor (driven gear) 3 are respectively rotatably disposed in a gear housing chamber (not shown) defined by the pump housing. In addition, the gear pump 1 may...
PUM
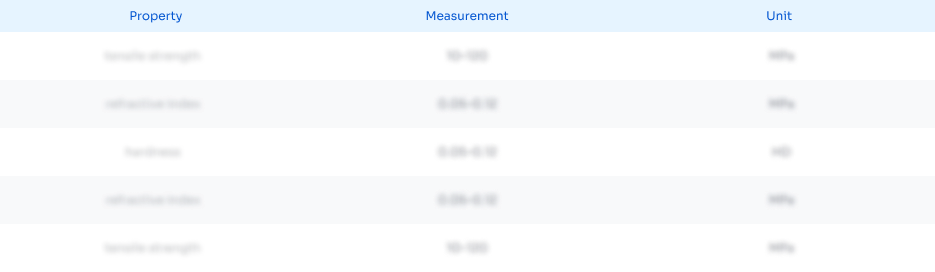
Abstract
Description
Claims
Application Information

- R&D
- Intellectual Property
- Life Sciences
- Materials
- Tech Scout
- Unparalleled Data Quality
- Higher Quality Content
- 60% Fewer Hallucinations
Browse by: Latest US Patents, China's latest patents, Technical Efficacy Thesaurus, Application Domain, Technology Topic, Popular Technical Reports.
© 2025 PatSnap. All rights reserved.Legal|Privacy policy|Modern Slavery Act Transparency Statement|Sitemap|About US| Contact US: help@patsnap.com