Dynamic control method of linear steering engine electric loading system
A loading system and dynamic control technology, applied in the direction of computer control, program control, general control system, etc., can solve the problems of unmeasurable linear steering gear loading, affecting loading accuracy, weakly damped pneumatic system, etc., to shorten the dynamic tracking process. , Guarantee force tracking accuracy, improve the effect of loading accuracy
- Summary
- Abstract
- Description
- Claims
- Application Information
AI Technical Summary
Problems solved by technology
Method used
Image
Examples
Embodiment 1
[0110] In order to verify the present invention, the components selected in the embodiment are shown in Table 1, and the parameters of the electric loading system of the linear steering gear are shown in Table 2.
[0111] Table 1 Selection of each component of the test bench
[0112]
[0113]
[0114] Table 2 System parameters
[0115] parameter
parameter value
unit
significance
K t
1.75
Nm / A
Electromagnetic torque constant
K e
112
V / Krpm
back emf constant
K L
6000
Nm / rad
elastic stiffness constant
J L
8.81×10 -5
Kgm 2
load moment of inertia
L m
11.4
mH
Inductance constant
R m
2.1
Ω
Stator winding resistance
J m
9.1×10 -4
Kgm 2
Moment of inertia of PMSM
B m
0.052
Nm / Krpm
Motor damping constant
P
25
mm
screw lead
[0116] Secondly, to analyze whether the system is stable, use MATLAB...
PUM
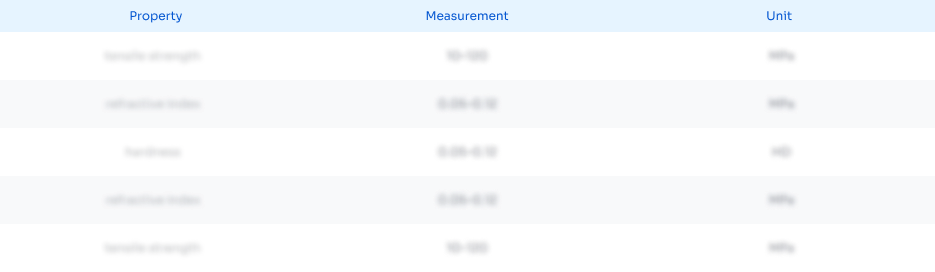
Abstract
Description
Claims
Application Information

- R&D
- Intellectual Property
- Life Sciences
- Materials
- Tech Scout
- Unparalleled Data Quality
- Higher Quality Content
- 60% Fewer Hallucinations
Browse by: Latest US Patents, China's latest patents, Technical Efficacy Thesaurus, Application Domain, Technology Topic, Popular Technical Reports.
© 2025 PatSnap. All rights reserved.Legal|Privacy policy|Modern Slavery Act Transparency Statement|Sitemap|About US| Contact US: help@patsnap.com