A Welding Process for the End Flange of a Prestressed Bimetallic Centrifugal Casting Composite Pipe
A technology of centrifugal casting and pre-compressive stress, which is applied in the direction of metal processing equipment, welding equipment, manufacturing tools, etc., can solve the problems of separation and cracking of double metal layers, and achieve the effect of enhancing compressive stress
- Summary
- Abstract
- Description
- Claims
- Application Information
AI Technical Summary
Problems solved by technology
Method used
Image
Examples
Embodiment Construction
[0039] Below in conjunction with accompanying drawing and specific embodiment the present invention will be described in further detail:
[0040] The prestressed bimetallic centrifugal casting composite pipe is composed of a high chromium cast iron inner layer and a stainless steel outer layer. The flange material is 20 steel. The welding position is shown in figure 1 . In the figure, prestressed bimetallic centrifugal casting composite pipe 1, flange 2, annular fillet weld 3, and the welding process of the prestressed bimetallic centrifugal casting composite pipe end flange The specific welding process is as follows:
[0041] 1. Calculation of the theoretical preheating temperature of the flange: use the following formula to calculate the theoretical preheating problem T of the flange:
[0042]
[0043] In the formula, μ——stiffness coefficient;
[0044] D - the inner diameter of the flange;
[0045] alpha 1 - thermal expansion coefficient of stainless steel;
[0046]...
PUM
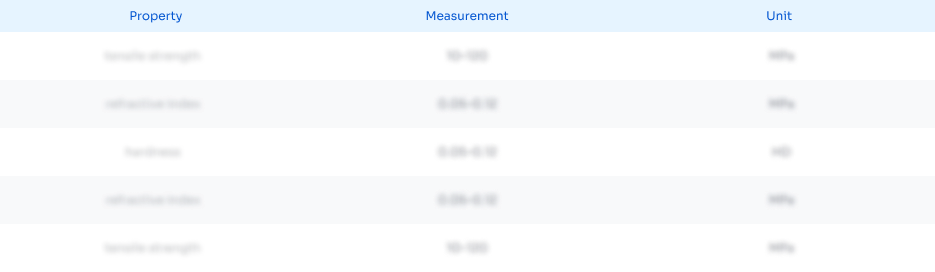
Abstract
Description
Claims
Application Information

- R&D Engineer
- R&D Manager
- IP Professional
- Industry Leading Data Capabilities
- Powerful AI technology
- Patent DNA Extraction
Browse by: Latest US Patents, China's latest patents, Technical Efficacy Thesaurus, Application Domain, Technology Topic, Popular Technical Reports.
© 2024 PatSnap. All rights reserved.Legal|Privacy policy|Modern Slavery Act Transparency Statement|Sitemap|About US| Contact US: help@patsnap.com