Dewatering drying method for fine slag slurry in coal gasification system and dewatering drying system used by dewatering drying method
A technology of coal gasification and fine slag, which is applied in chemical instruments and methods, separation methods, water/sewage treatment, etc., can solve the problem of drying treatment of fine slag slurry with low waste heat utilization rate, reduce the waste heat utilization rate of low-pressure flash steam, and cannot directly As a boiler fuel, etc., it can improve energy utilization efficiency, reduce equipment investment costs, and reduce costs.
- Summary
- Abstract
- Description
- Claims
- Application Information
AI Technical Summary
Problems solved by technology
Method used
Image
Examples
Embodiment 1
[0034] Embodiment 1 slag water concentration and dehydration drying system
[0035] figure 1 Shown is the schematic flow chart of the slag water concentration and fine slag slurry dehydration and drying of the coal gasification system of the preferred embodiment of the present invention, wherein the low-pressure flash evaporator 1, the vacuum flash evaporator 2 and the settling tank 3 form the slag water concentration unit, and the air heating Device 4, hydrocyclone 5, spray dryer 6, condenser 7, separator 8 and vacuum pump 9 form a fine slag slurry dehydration drying unit.
[0036] In the slag water concentration unit, the slag water S1 produced by the coal gasification system (the concentrated black water of the evaporative hot water tower) is flashed through the low-pressure flash evaporator 1 to generate the low-pressure flash concentrated black water S2 and the low-pressure flash steam S3; the low-pressure flash concentrated black water The water S2 is flashed through th...
Embodiment 2
[0038] The treatment of the slag water that embodiment 2 coal-water slurry gasification plant produces
[0039] The slag water produced by a certain coal-water slurry gasification device using coal as raw material is processed through the slag water concentration and dehydration drying system of Example 1, wherein the fine slag slurry S6 obtained by the settling tank has a solid content of 20%, and the fine slag is controlled The processing capacity of the slurry S6 is 8630.0kg / h, and 4884kg / h of low-pressure flash steam S3 is extracted as the heat source of the air heater 4 . The main logistics data of the treatment process in this embodiment are shown in Table 1.
[0040] Table 1 embodiment 2 main logistics parameters
[0041]
[0042] As can be seen from Table 1, adopt processing method of the present invention, this embodiment can reach following beneficial effect:
[0043]1. In this embodiment, the low-pressure flash steam S3 is used as the heat source of the air hea...
Embodiment 3
[0046] Embodiment 3 Treatment of slag water produced by pulverized coal gasification unit
[0047] The slag water produced by a pulverized coal gasification device using coal as raw material is processed through the slag water concentration and dehydration drying system of Example 1, wherein the fine slag slurry S6 obtained by the settling tank has a solid content of 15%, and the fine slag slurry S6 is controlled The processing capacity is 8630.0kg / h, and 3307kg / h low-pressure flash steam S3 is extracted as the heat source of the air heater 4 . The main logistics data of the treatment process in this embodiment are shown in Table 2.
[0048] Table 2 embodiment 3 main logistics parameters
[0049]
[0050] As can be seen from Table 2, adopt processing method of the present invention, this embodiment can reach following beneficial effect:
[0051] 1. In this embodiment, the low-pressure flash steam S3 is used as the heat source of the air heater 4 to heat the air S10, and t...
PUM
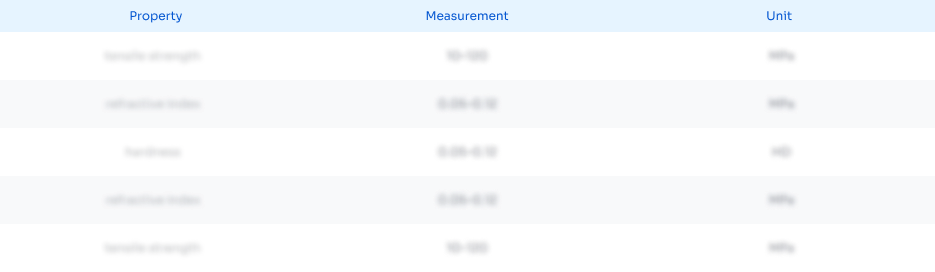
Abstract
Description
Claims
Application Information

- R&D Engineer
- R&D Manager
- IP Professional
- Industry Leading Data Capabilities
- Powerful AI technology
- Patent DNA Extraction
Browse by: Latest US Patents, China's latest patents, Technical Efficacy Thesaurus, Application Domain, Technology Topic, Popular Technical Reports.
© 2024 PatSnap. All rights reserved.Legal|Privacy policy|Modern Slavery Act Transparency Statement|Sitemap|About US| Contact US: help@patsnap.com