Preparation method and uses of iron-tannic acid skeleton modified composite film
A tannic acid and composite membrane technology, applied in separation methods, chemical instruments and methods, membrane technology, etc., can solve the problems of secondary pollution, frequent use, non-degradable organic matter, etc. Contamination, the effect of excellent separation
- Summary
- Abstract
- Description
- Claims
- Application Information
AI Technical Summary
Problems solved by technology
Method used
Image
Examples
Embodiment 1
[0026] step 1:
[0027] A 2×2cm stainless steel mesh was ultrasonically cleaned with acetone and absolute ethanol, dried, and impregnated in 20mL Fe 3+ and TA mixed solution, where Fe 3+ A mixed solution with a concentration of 1.0mg / mL and a concentration of TA of 1.0mg / mL was reacted for 3 minutes, then dried in an oven at 50°C for 3 minutes; Fe III -TA-1 modified composite membrane, the iron salt is Fe(NO 3 ) 3 9H 2 O.
[0028] Step 2:
[0029] Fe will be produced III -TA-1 modified composite membrane is fixed to the self-made oil-water separation device, wet the surface of the omentum with a small amount of distilled water, and then pour 100mL of a mixed solution of hexane and water with a volume ratio of 1:1 into the built device . In order to more accurately determine the oil-water separation efficiency of the composite membrane, the samples were divided into three parts, and each sample was tested three times. The whole experiment process was carried out under ...
Embodiment 2
[0034] step 1:
[0035] A 2×2cm stainless steel mesh was ultrasonically cleaned with acetone and absolute ethanol, dried, and impregnated in 20mL Fe 3+ and TA mixed solution, where Fe 3+ A mixed solution with a concentration of 5.0mg / mL and a concentration of TA of 5.0mg / mL was reacted for 3 minutes, then dried in an oven at 50°C for 3 minutes; 5Fe III -5TA-1 modified composite membrane.
[0036] Step 2:
[0037] 5Fe will be produced III -5TA-1 modified composite membrane was fixed to a self-made oil-water separation device, and the oil-water separation experiment was carried out according to the operation of step 2 in Example 1. The experimental results showed that the oil-water separation efficiency was 99.0%.
Embodiment 3
[0039] step 1:
[0040] A 2×2cm stainless steel mesh was ultrasonically cleaned with acetone and absolute ethanol, dried, and impregnated in 20mL Fe 3+ and TA mixed solution, where Fe 3+ A mixed solution with a concentration of 15mg / mL and a TA concentration of 15mg / mL was reacted for 3 minutes, then dried in an oven at 50°C for 3 minutes; 15Fe III -15TA-1 modified composite membrane.
[0041] Step 2:
[0042] 15Fe will be produced III -15TA-1 modified composite membrane was fixed to a self-made oil-water separation device, and the oil-water separation experiment was carried out according to the operation of step 2 in Example 1, and toluene was used instead of hexane. The experimental results showed that the oil-water separation efficiency was 98.8%.
PUM
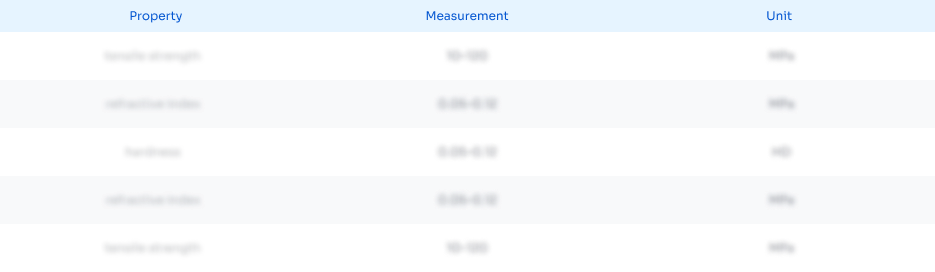
Abstract
Description
Claims
Application Information

- Generate Ideas
- Intellectual Property
- Life Sciences
- Materials
- Tech Scout
- Unparalleled Data Quality
- Higher Quality Content
- 60% Fewer Hallucinations
Browse by: Latest US Patents, China's latest patents, Technical Efficacy Thesaurus, Application Domain, Technology Topic, Popular Technical Reports.
© 2025 PatSnap. All rights reserved.Legal|Privacy policy|Modern Slavery Act Transparency Statement|Sitemap|About US| Contact US: help@patsnap.com