Steel tube machining method with high yield
A processing method and technology of yield rate, applied in the field of steel pipe processing with high yield rate, can solve problems such as low yield rate, achieve high quality, stable performance, and increase the elongation coefficient
- Summary
- Abstract
- Description
- Claims
- Application Information
AI Technical Summary
Problems solved by technology
Method used
Examples
Embodiment 1
[0035] Using continuous casting steel billet as raw material, the billet is uniformly heated to 1300°C for 3 hours to ensure uniform heating of the billet;
[0036] Perforation: punch the center hole on the heat pipe blank, and then perforate; the perforation temperature is 1000°C;
[0037] Machining: Machining on the surface of the tube blank and its machining cutting depth are controlled within the range that can remove casting defects on the surface of the tube blank;
[0038] annealing:
[0039] The first annealing: the tube billet after machining is put into the annealing furnace, the temperature rises to 750°C, and the temperature is kept for 1h;
[0040] The second annealing: raise the temperature in the furnace to 800°C and keep it warm for 3 hours;
[0041] The third annealing: lower the temperature in the furnace to 740°C and keep it warm for 1h;
[0042] The fourth annealing: reduce the temperature in the furnace to 680°C and keep it for 1h;
[0043] Pickling: T...
Embodiment 2
[0050] Heating: Using continuous casting billet as raw material, the billet is evenly heated to 1350°C, and the heating time is 3.5 hours, so as to ensure uniform heating of the billet;
[0051] Perforation: punch the center hole on the heat pipe blank, and then perforate; the perforation temperature is 1100°C;
[0052] Machining: Machining on the surface of the tube blank and its machining cutting depth are controlled within the range that can remove casting defects on the surface of the tube blank;
[0053] annealing:
[0054] The first annealing: put the machined tube billet into the annealing furnace, raise the temperature to 755°C, and keep it warm for 1.2h;
[0055] The second annealing: raise the temperature in the furnace to 810°C and keep it warm for 3.2h;
[0056] The third annealing: lower the temperature in the furnace to 755°C and keep it warm for 1.4h;
[0057] The fourth annealing: lower the temperature in the furnace to 690°C and keep it warm for 1.5h;
[0...
Embodiment 3
[0065] Heating: Using continuous casting steel billet as raw material, the billet is uniformly heated to 1400°C, and the heating time is 4 hours, so as to ensure uniform heating of the billet;
[0066] Perforation: punch a central hole on the heat pipe blank, and then perforate; the perforation temperature is 1200°C;
[0067] Machining: Machining on the surface of the tube blank and its machining cutting depth are controlled within the range that can remove casting defects on the surface of the tube blank;
[0068] annealing:
[0069] The first annealing: put the tube blank after machining into the annealing furnace, raise the temperature to 760°C, and keep it for 1.3h;
[0070] The second annealing: raise the temperature in the furnace to 820°C for 3.5 hours;
[0071] The third annealing: lower the temperature in the furnace to 770°C and keep it warm for 8h;
[0072] The fourth annealing: lower the temperature in the furnace to 700°C and keep it warm for 2 hours;
[0073]...
PUM
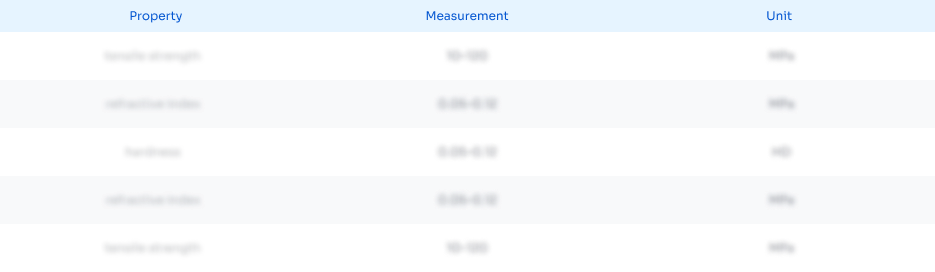
Abstract
Description
Claims
Application Information

- R&D
- Intellectual Property
- Life Sciences
- Materials
- Tech Scout
- Unparalleled Data Quality
- Higher Quality Content
- 60% Fewer Hallucinations
Browse by: Latest US Patents, China's latest patents, Technical Efficacy Thesaurus, Application Domain, Technology Topic, Popular Technical Reports.
© 2025 PatSnap. All rights reserved.Legal|Privacy policy|Modern Slavery Act Transparency Statement|Sitemap|About US| Contact US: help@patsnap.com