Blue MOFs/cast nylon nanometer composite material as well as preparation method and application thereof
A technology of nanocomposite materials and cast nylon, which is applied in the field of blue MOFs/cast nylon nanocomposites and its preparation, can solve the problems of low performance, polymerization inhibition, uneven material color, etc., and achieve good strength and toughness, and good comprehensive performance , The effect of simple preparation process
- Summary
- Abstract
- Description
- Claims
- Application Information
AI Technical Summary
Problems solved by technology
Method used
Image
Examples
Embodiment 1
[0046] The material ratio in Table 1 is selected, and the blue MOFs are Cu(BDC)MOF.
[0047] S1. Add the blue MOFs and the aprotic polar solvent according to the above ratio into the kettle A containing the caprolactam monomer 1, adjust the temperature of the kettle A to 70-85°C, and carry out the stirring reaction for 0.5-2 hours;
[0048] S2. Warm up the kettle A in step S1 to 130-140° C., and vacuumize for 15-60 minutes under a certain degree of vacuum. The vacuum degree of the vacuum-evacuation is 99000-99997 Pa; then add an initiator to react in a vacuum for 15-30 minutes;
[0049] S3. Put the caprolactam monomer 2 into the kettle B, heat until the caprolactam monomer 2 melts and start vacuuming, the caprolactam monomer 2 is completely melted, add the catalyst and heat up to 130-140°C, and continue vacuuming for 10-15 minutes;
[0050] S4. After mixing the materials obtained in kettle A and kettle B, pour them into a mold at 150-170°C for polymerization and molding, react...
Embodiment 2
[0053] The material ratio in Table 1 is selected. The difference of Example 1 is that the raw material is Cu2(BDC)2(DABCD) for the blue MOFs, and the preparation process is the same as that of Example 1.
[0054] The properties of the prepared blue MOFs / cast nylon nanocomposites are shown in Table 2.
Embodiment 3
[0056] The material ratio in Table 1 is selected, and the difference of Example 1 is that the raw material is Cu2(NDC)2(DABCO) for the blue MOFs, and the preparation process is the same as that of Example 1.
[0057] The properties of the prepared blue MOFs / cast nylon nanocomposites are shown in Table 2.
PUM
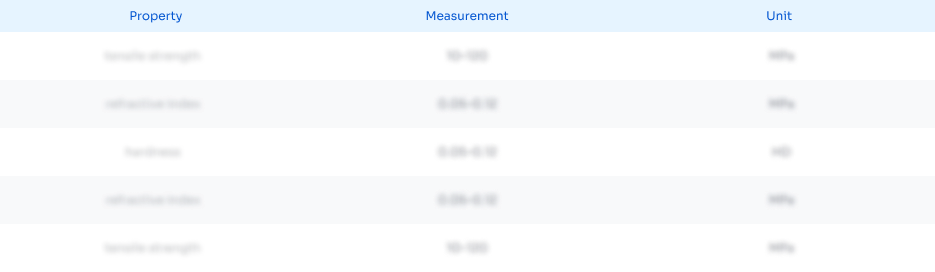
Abstract
Description
Claims
Application Information

- R&D Engineer
- R&D Manager
- IP Professional
- Industry Leading Data Capabilities
- Powerful AI technology
- Patent DNA Extraction
Browse by: Latest US Patents, China's latest patents, Technical Efficacy Thesaurus, Application Domain, Technology Topic, Popular Technical Reports.
© 2024 PatSnap. All rights reserved.Legal|Privacy policy|Modern Slavery Act Transparency Statement|Sitemap|About US| Contact US: help@patsnap.com