Autoclaved aerated concrete block prepared from natural granite chips and preparation method of autoclaved aerated concrete block
A technology of concrete block and autoclaved aeration, which is applied in the field of building wall materials, can solve the problems of no major advantages, low added value of products, and influence on the enthusiasm for sand control with sand, and achieves high rigidity, low cost, and improved efficiency. The effect of construction efficiency
- Summary
- Abstract
- Description
- Claims
- Application Information
AI Technical Summary
Problems solved by technology
Method used
Examples
Embodiment 1
[0027] An autoclaved aerated concrete (AAC) block prepared by using natural granite chips. The weight ratio of the basic material components of the concrete slab body is: 2800kg of natural granite chips, 600kg of cement, 520kg of quicklime, 75kg of slaked lime, Desulfurization gypsum 147kg, aluminum powder 2.0kg, acacia powder 0.08kg. The SiO2 content in the natural granite chips is between 60% and 75%, the organic matter is not higher than 1.5%, and the mud content is not higher than 0.5%. The cement is P.O42.5 cement; the aluminum powder paste is oil-type aluminum powder.
[0028] The method for preparing the above-mentioned autoclaved aerated concrete (AAC) block prepared from natural granite chips comprises the following steps:
[0029] 1) Use a ball mill to grind natural granite chips with a moisture content of less than 4% until the fineness is 0.08mm, and the sieve residue on the square hole sieve is no more than 10%; after crushing the quicklime with a jaw crusher, us...
Embodiment 2
[0037] The autoclaved aerated concrete slab prepared by using natural granite chips, the weight ratio of the basic material components of the concrete slab body is: 3500kg of natural granite chips, 700kg of cement, 620kg of quicklime, 120kg of slaked lime, 150kg of desulfurized gypsum, aluminum powder Cream 2.5kg, tea saponin 0.10kg. The SiO2 content in the natural granite chips is between 60% and 75%, the organic matter is not higher than 1.5%, and the mud content is not higher than 0.5%. The cement is P.O42.5 cement; the aluminum powder paste is oil-type aluminum powder.
[0038] The method for preparing the above-mentioned autoclaved aerated concrete (AAC) block prepared from natural granite chips comprises the following steps:
[0039]1) Use a ball mill to grind natural granite chips with a moisture content of less than 4% until the fineness is 0.08mm, and the sieve residue on the square hole sieve is no more than 10%; after crushing the quicklime with a jaw crusher, use ...
Embodiment 3
[0047] The autoclaved aerated concrete (AAC) block prepared by using natural granite chips, the weight ratio of the base material components of the autoclaved aerated concrete (AAC) block is: 2450kg of natural granite chips, 480kg of cement, Quicklime 420kg, slaked lime 30kg, desulfurization gypsum 42kg, aluminum powder paste 1.5kg, acacia powder 0.05kg. The SiO2 content in the natural granite chips is between 60% and 75%, the organic matter is not higher than 1.5%, and the mud content is not higher than 0.5%. The cement is P.O42.5 cement; the aluminum powder is oil-type aluminum powder.
[0048] The method for preparing the above-mentioned autoclaved aerated concrete (AAC) block prepared from natural granite chips comprises the following steps:
[0049] 1) Use a ball mill to grind natural granite chips with a moisture content of less than 4% until the fineness is 0.08mm, and the sieve residue on the square hole sieve is no more than 10%; after crushing the quicklime with a j...
PUM
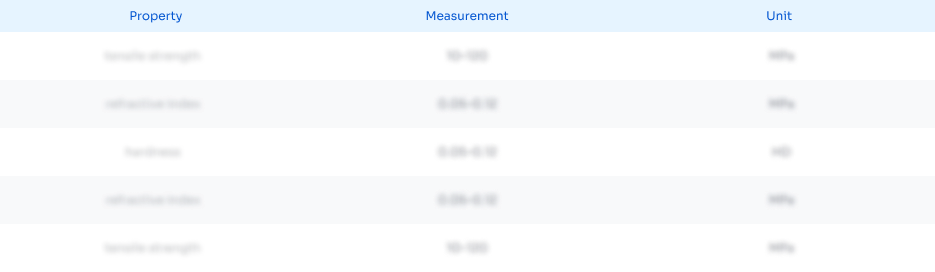
Abstract
Description
Claims
Application Information

- R&D Engineer
- R&D Manager
- IP Professional
- Industry Leading Data Capabilities
- Powerful AI technology
- Patent DNA Extraction
Browse by: Latest US Patents, China's latest patents, Technical Efficacy Thesaurus, Application Domain, Technology Topic, Popular Technical Reports.
© 2024 PatSnap. All rights reserved.Legal|Privacy policy|Modern Slavery Act Transparency Statement|Sitemap|About US| Contact US: help@patsnap.com