Insulating material for cable insulating layer and underwater composite cable
A cable insulation and composite cable technology, applied in the direction of insulators, power cables, insulated conductors, etc., can solve the problems recognized by the world as complex in manufacturing technology, and achieve the effects of stable internal layout, superior compressive strength, and excellent adaptability
- Summary
- Abstract
- Description
- Claims
- Application Information
AI Technical Summary
Problems solved by technology
Method used
Image
Examples
Embodiment 1
[0045] Embodiment 1: A kind of insulation material for cable insulation layer
[0046] S1. Weigh a certain amount of 36 parts of PVC resin, 17 parts of white carbon black, 14 parts of diphenyl ether resin, 9 parts of MBS resin, 14 parts of cresol-formaldehyde resin, 18 parts of linseed oil alkyd resin, fatty alcohol polyoxygen Add 3 parts of vinyl ether, 7 parts of calcium stearate, and 13 parts of calcined clay into the internal mixer, and knead at 18°C for 25 minutes;
[0047] S2. Continue to add 5 parts of toughening agent, 5 parts of antistatic agent, 4 parts of compatibilizer, 3-5 parts of antioxidant and 69 parts of deionized water in step S1. High-speed mixing and stirring reaction at 1100r / min for 2.5 hours;
[0048] S3. After mixing the product of step S2 evenly, put it into a sand mill and grind it to a fineness of 33 microns, and then discharge the product.
Embodiment 2
[0049] Embodiment 2: A kind of insulation material for cable insulation layer
[0050] S1. Weigh a certain amount of 38 parts of PVC resin, 18 parts of white carbon black, 14 parts of diphenyl ether resin, 11 parts of MBS resin, 15 parts of cresol-formaldehyde resin, 19 parts of linseed oil alkyd resin, fatty alcohol polyoxygen Add 4 parts of vinyl ether, 9 parts of calcium stearate, and 14 parts of calcined clay into the internal mixer, and knead at 300°C for 30 minutes;
[0051] S2. Continue to add 6 parts of toughening agent, 6 parts of antistatic agent, 5 parts of compatibilizer, 5 parts of antioxidant and 76 parts of deionized water in step S1. At a temperature of 100 °C, the stirring speed is 1200 r / Min under high-speed mixing and stirring reaction for 3 hours;
[0052] S3. After mixing the product of step S2 evenly, put it into a sand mill and grind it to a fineness of 35 microns, and then discharge the product.
Embodiment 3
[0053] Embodiment 3: A kind of insulation material for cable insulation layer
[0054] S1. Weigh a certain amount of 32 parts of PVC resin, 16 parts of white carbon black, 11 parts of diphenyl ether resin, 9 parts of MBS resin, 12 parts of cresol-formaldehyde resin, 16 parts of linseed oil alkyd resin, fatty alcohol polyoxygen Add 3 parts of vinyl ether, 6 parts of calcium stearate, and 11 parts of calcined clay into the internal mixer, and knead at 150°C for 20 minutes;
[0055] S2. Continue to add 4 parts of toughening agent, 4 parts of antistatic agent, 3 parts of compatibilizer, 3 parts of antioxidant and 65 parts of deionized water in step S1. At a temperature of 80 °C, the stirring rate is 1000 r / Min under high-speed mixing and stirring reaction for 2 hours;
[0056] S3. After mixing the product of step S2 evenly, put it into a sand mill and grind it to a fineness of 25 microns, and then discharge the product.
PUM
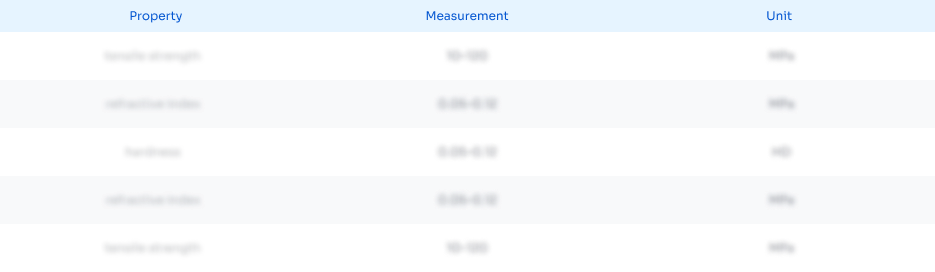
Abstract
Description
Claims
Application Information

- Generate Ideas
- Intellectual Property
- Life Sciences
- Materials
- Tech Scout
- Unparalleled Data Quality
- Higher Quality Content
- 60% Fewer Hallucinations
Browse by: Latest US Patents, China's latest patents, Technical Efficacy Thesaurus, Application Domain, Technology Topic, Popular Technical Reports.
© 2025 PatSnap. All rights reserved.Legal|Privacy policy|Modern Slavery Act Transparency Statement|Sitemap|About US| Contact US: help@patsnap.com