A method for repairing an aero-engine composite casing
An aero-engine and composite material technology, applied in the field of composite material repair, can solve the problems of waste of resources, large casing volume, complex structure and shape, etc., and achieve the effect of preventing further expansion and simple process
- Summary
- Abstract
- Description
- Claims
- Application Information
AI Technical Summary
Problems solved by technology
Method used
Image
Examples
Embodiment 2
[0049] When a certain type of aero-engine was being repaired, it was found that there was an ablation area on the inner surface of the casing, and the ablation penetrated in the thickness direction, and the inner surface and the outer surface were simultaneously repaired according to the method provided by the present invention. The specific operation steps are as follows:
[0050] S1. Check the degree of damage to the composite casing, and measure the size and shape of the defect. The size of the damaged area is about 90 mm×40 mm, and it penetrates in the thickness direction. The schematic diagram is as follows Figure 7 shown.
[0051] S2. Carry out smooth transition grinding on the damaged area with a rotating grinding head, remove the damaged area, the grinding depth is about 1.4mm, wash with acetone and then dry. The depth of the defect exceeds half of the original thickness (2 mm), so repairs with metal reinforcement sheets are required on both sides. Drill 6 holes evenl...
PUM
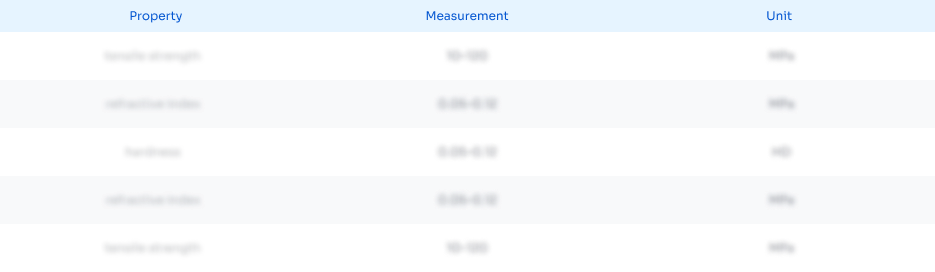
Abstract
Description
Claims
Application Information

- R&D Engineer
- R&D Manager
- IP Professional
- Industry Leading Data Capabilities
- Powerful AI technology
- Patent DNA Extraction
Browse by: Latest US Patents, China's latest patents, Technical Efficacy Thesaurus, Application Domain, Technology Topic, Popular Technical Reports.
© 2024 PatSnap. All rights reserved.Legal|Privacy policy|Modern Slavery Act Transparency Statement|Sitemap|About US| Contact US: help@patsnap.com