Low refractive layer and anti-reflection film comprising same
A low-refraction and satisfying technology, applied in coatings, optics, instruments, etc., can solve the problems of interlayer adhesion (weakened interface adhesion, high production cost, and reduced alkali resistance of polymer films, etc., to achieve excellent optics and Mechanical properties, anti-glare effect
- Summary
- Abstract
- Description
- Claims
- Application Information
AI Technical Summary
Problems solved by technology
Method used
Image
Examples
preparation example 1
[0132] Preparation Example 1: Preparation of Hard Coating Film 1 (HD1)
[0133] A salt-type antistatic hard coating solution (manufactured by KYOEISHA Chemical Co., Ltd., solid content: 50% by weight, trade name: LJD-1000) was coated on a triacetylcellulose film with a #10mayer rod and placed on the Dry at 90°C for 1 minute, then use 150mJ / cm 2 A hard coating film (HD1) with a thickness of 5 μm was prepared by irradiating with ultraviolet light.
preparation example 2
[0134] Preparation Example 2: Preparation of Hard Coat 2 (HD2)
[0135] 30 g of pentaerythritol triacrylate, 2.5 g of a high molecular weight copolymer (BEAMSET 371, Arakawa Corporation, epoxy acrylate, molecular weight: 40,000), 20 g of methyl ethyl ketone, and 0.5 g of a leveling agent (Tego wet270) were uniformly mixed. Then, 2 g of an acrylic-styrene copolymer having a refractive index of 1.525 (volume average particle diameter: 2 μm, manufactured by Sekisui Plastic) was added as fine particles to the mixture to prepare a hard coating composition. The hardcoat composition thus obtained was coated onto a triacetylcellulose film with a #10 mayer rod and dried at 90°C for 1 minute. Use 150mJ / cm 2 The dried product was irradiated with ultraviolet light to prepare a hard coating film (HD2) with a thickness of 5 μm.
preparation example 3
[0136] Preparation Example 3: Preparation of Polysilsesquioxane 1
[0137] Add 36.57 g (0.156 mol) of isooctyltrimethoxysilane, 23.34 g (0.094 mol) of 3-methacryloxypropyltrimethoxysilane, and 500 mL of methanol to a tank equipped with a nitrogen inlet tube, condenser, and stirring in a 1 L reactor and stirred at room temperature for 10 min. Then, tetramethylammonium hydroxide (280 g, 0.77 mol, 25% by weight in methanol) was added thereto, and a reaction was performed for 8 hours by raising the reactor temperature to 60° C. under a nitrogen atmosphere. After the reaction was completed, 15 g of polyhedral oligomeric silsesquioxane (POSS) substituted with isooctyl and methacryloxypropyl groups were obtained by column chromatography and recrystallization. Validation results of GP chromatography showed that the molar ratio of methacryloxypropyl to isooctyl substituted at the silicon of polysilsesquioxane (moles of methacryloxypropyl / isooctyl The number of moles) is about 0.6 to ...
PUM
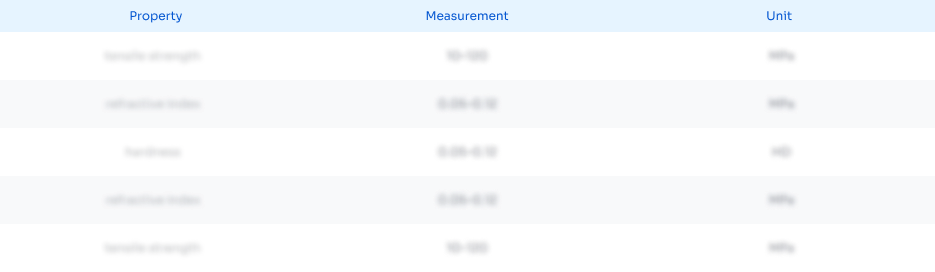
Abstract
Description
Claims
Application Information

- R&D
- Intellectual Property
- Life Sciences
- Materials
- Tech Scout
- Unparalleled Data Quality
- Higher Quality Content
- 60% Fewer Hallucinations
Browse by: Latest US Patents, China's latest patents, Technical Efficacy Thesaurus, Application Domain, Technology Topic, Popular Technical Reports.
© 2025 PatSnap. All rights reserved.Legal|Privacy policy|Modern Slavery Act Transparency Statement|Sitemap|About US| Contact US: help@patsnap.com