Smelting system for alloy
A technology of alloy and smelting furnace, which is applied in the field of smelting system for alloys, can solve the problem of uncontrollable cooling rate and achieve the effect of cost saving
- Summary
- Abstract
- Description
- Claims
- Application Information
AI Technical Summary
Problems solved by technology
Method used
Image
Examples
Embodiment Construction
[0032] As shown in the figure, the specific implementation method is as follows:
[0033] A smelting system for alloys, comprising a smelting furnace 2, a cooling furnace 11 and a base 8 arranged sequentially from top to bottom, an upper cover 214 is set on the top of the smelting furnace, and a control system 1 for controlling the operation of the entire system is set on the base 8 The smelting furnace 2 includes a smelting cavity and a heat preservation cavity arranged in sequence from top to bottom. The smelting furnace 2 is connected with a vacuum system 4 that provides a vacuum smelting environment for the smelting cavity and an intake and exhaust solenoid valve 3 that controls the opening and closing of the vacuum system. A mold 5 for cooling and forming the alloy is also provided in the heat preservation chamber of the furnace 2, and a channel connecting the heat preservation chamber of the smelting furnace 2 and the cooling furnace 11 is provided directly below the mold...
PUM
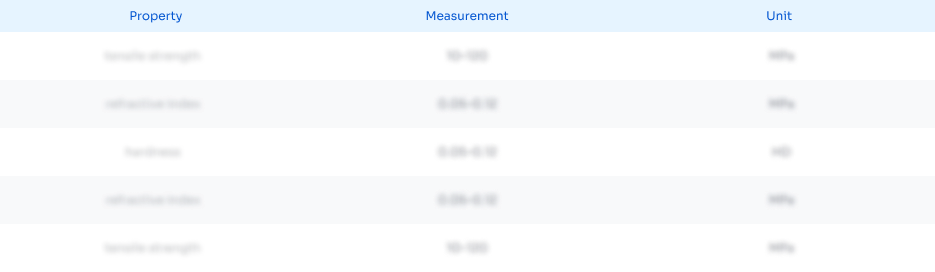
Abstract
Description
Claims
Application Information

- R&D
- Intellectual Property
- Life Sciences
- Materials
- Tech Scout
- Unparalleled Data Quality
- Higher Quality Content
- 60% Fewer Hallucinations
Browse by: Latest US Patents, China's latest patents, Technical Efficacy Thesaurus, Application Domain, Technology Topic, Popular Technical Reports.
© 2025 PatSnap. All rights reserved.Legal|Privacy policy|Modern Slavery Act Transparency Statement|Sitemap|About US| Contact US: help@patsnap.com