Particle filling valve
A filling valve and granule technology, which is applied in packaging, bottle filling, liquid bottling, etc., can solve the problems of slow feeding speed, poor cleaning effect, small width, etc., so as to improve feeding speed, filling quality, The effect of improving filling efficiency
- Summary
- Abstract
- Description
- Claims
- Application Information
AI Technical Summary
Problems solved by technology
Method used
Image
Examples
Embodiment Construction
[0012] The present invention will be further described below in conjunction with the accompanying drawings and specific embodiments.
[0013] like figure 2 , image 3 As shown, the described particle filling valve includes an upper valve seat 1 and a lower valve seat 2, the upper valve seat 1 is provided with a first inner cavity 3 axially penetrating the upper valve seat 1, and the upper valve seat The side wall of 1 is provided with a feed hole 4 communicating with the first inner chamber 3, and a second inner chamber 5 axially penetrating the lower valve seat 2 is arranged in the lower valve seat 2, and the bottom of the lower valve seat 2 is downward An integral extension has a tubular filling nozzle 7 whose interior communicates with the second inner cavity 5 and can be inserted into the mouth of the bottle 6. A bottle mouth sealing ring 8 is sleeved outside the tubular filling nozzle 7. The upper valve seat 1 is connected with the lower valve seat 2 through the flexib...
PUM
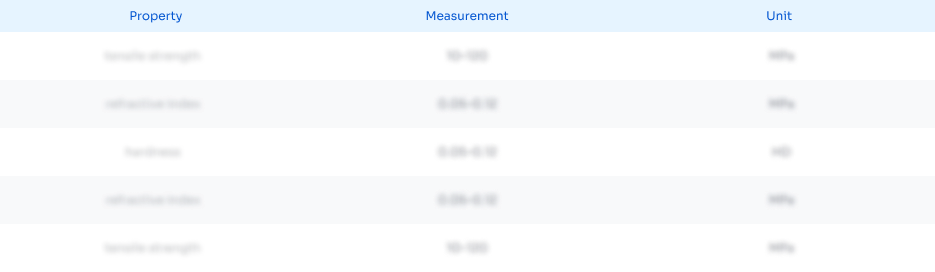
Abstract
Description
Claims
Application Information

- Generate Ideas
- Intellectual Property
- Life Sciences
- Materials
- Tech Scout
- Unparalleled Data Quality
- Higher Quality Content
- 60% Fewer Hallucinations
Browse by: Latest US Patents, China's latest patents, Technical Efficacy Thesaurus, Application Domain, Technology Topic, Popular Technical Reports.
© 2025 PatSnap. All rights reserved.Legal|Privacy policy|Modern Slavery Act Transparency Statement|Sitemap|About US| Contact US: help@patsnap.com