A wire cutting and grinding machine
A technology of wire cutting and integrated machine, which is applied in the field of mechanical processing, can solve the problems of increasing the substrate grinding allowance, increasing the grinding time, and large cutting allowance, so as to reduce processing steps, improve automation, and reduce wear and tear. Effect
- Summary
- Abstract
- Description
- Claims
- Application Information
AI Technical Summary
Problems solved by technology
Method used
Image
Examples
Embodiment approach
[0032] As an embodiment of the present invention, the adjustment unit 31 includes an adjustment box 311, a No. 1 screw 312, a No. 2 screw 313, a cover plate 314, a No. 3 servo motor 315, a coupling 316, a screw 317 and a positioning slide Block 318, the adjusting box body 311 is detachably fixed in the round hole of the support block 33, the left and right sides of the inner wall of the adjusting box body 311 are symmetrically provided with chute; the cover plate 314 is fixed on the adjusting box body 311 by the No. 1 screw 312; The No. 3 servo motor 315 is fixed on the cover plate 314 by the No. 2 screw 313, and the No. 3 servo motor 315 is used to provide the sliding power of the positioning slider 318; the screw rod 317 is threadedly connected with the positioning slider 318, and the screw rod 317 is passed through a coupling 316 is connected with the motor, and the screw rod 317 is used to transmit the power provided by the No. 3 servo motor 315; the positioning slider 318 ...
PUM
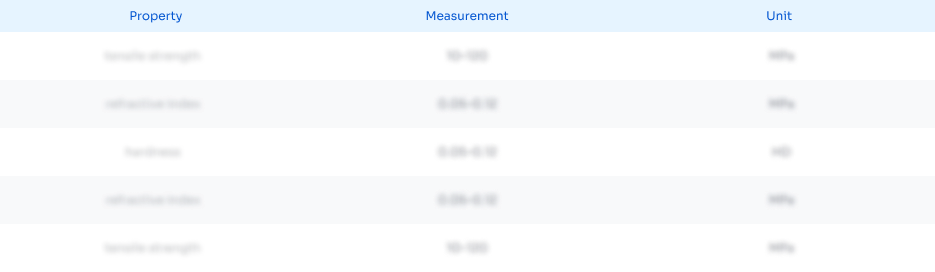
Abstract
Description
Claims
Application Information

- R&D
- Intellectual Property
- Life Sciences
- Materials
- Tech Scout
- Unparalleled Data Quality
- Higher Quality Content
- 60% Fewer Hallucinations
Browse by: Latest US Patents, China's latest patents, Technical Efficacy Thesaurus, Application Domain, Technology Topic, Popular Technical Reports.
© 2025 PatSnap. All rights reserved.Legal|Privacy policy|Modern Slavery Act Transparency Statement|Sitemap|About US| Contact US: help@patsnap.com