Preparation method of multilayer titanium-nickel alloy filter film
A technology of titanium-nickel alloy and filter membrane, which is applied in the field of nano-scale porous metal filter media and its preparation, can solve the problems of slow heating rate, alloy densification, difficulty in obtaining high-porosity porous titanium-nickel alloy, etc., and achieves low cost , good flexibility and high strength
- Summary
- Abstract
- Description
- Claims
- Application Information
AI Technical Summary
Problems solved by technology
Method used
Image
Examples
Embodiment Construction
[0019] Under nitrogen protection, high-purity carbonyl nickel powder (median diameter 6.7 μm) and ultrafine titanium hydride powder (median diameter 5.2 μm) were mixed for 12 hours in a V-shaped mixer at a mass ratio of 55:45; 8.0g of 32000 polyvinyl butyral was dissolved in 80mL of absolute ethanol by ultrasonic at 40°C, and magnetically stirred for 35min; Mix with the film-forming slurry, and stir under magnetic force for 80 minutes. Take 6g of film slurry, adjust the pressure of the film forming device to 0.8kPa, coat the surface of the quartz plate evenly, transfer it to a nitrogen atmosphere after there are no bubbles on the surface of the film, and let it stand and dry at 40°C for 4.5 hours to form a single-layer titanium-nickel alloy prefabricated film ; Use zinc stearate intervals to continue the second and third layers of coating process. After the upper layer of raw film is dry, control the speed to remove the film, and place it in a vacuum sintering furnace for sin...
PUM
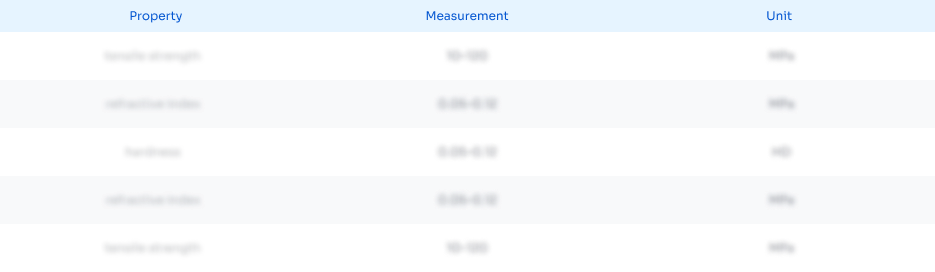
Abstract
Description
Claims
Application Information

- Generate Ideas
- Intellectual Property
- Life Sciences
- Materials
- Tech Scout
- Unparalleled Data Quality
- Higher Quality Content
- 60% Fewer Hallucinations
Browse by: Latest US Patents, China's latest patents, Technical Efficacy Thesaurus, Application Domain, Technology Topic, Popular Technical Reports.
© 2025 PatSnap. All rights reserved.Legal|Privacy policy|Modern Slavery Act Transparency Statement|Sitemap|About US| Contact US: help@patsnap.com