A kind of phase-change heat dissipation motor casing and air-cooled motor for its application
A phase change and chassis technology, applied in the direction of chassis/cover/support, electromechanical devices, electrical components, etc., can solve the problem of non-compliance with the lightweight and high power density of new energy vehicles, the increase in the weight of automotive motors, and the power density. Reduce and other problems to achieve the effect of improving heat dissipation effect, temperature balance, and fast internal heat transfer
- Summary
- Abstract
- Description
- Claims
- Application Information
AI Technical Summary
Problems solved by technology
Method used
Image
Examples
Embodiment 1
[0032] Such as Figure 1 to Figure 4 As shown, this embodiment provides a phase-change heat dissipation motor casing, including an annular casing 1, and a plurality of cooling fins 2 arranged at intervals protrude from the outside of the annular casing 1 along the circumferential direction, which is characterized in that: The heat dissipation fin 2 includes a fin body 21, and a plurality of vacuum phase change heat dissipation channels 22 are arranged in the fin body 21, and a phase change working fluid is arranged in the vacuum phase change heat dissipation channel 22.
[0033] The phase change heat dissipation motor housing described in this embodiment, through the phase change characteristics of the liquid working medium in a vacuum environment, enables the vacuum phase change heat dissipation channel 22 to have an extremely efficient heat transfer capacity, so that the heat in the annular shell 1 is rapidly The heat is transmitted to the end of the cooling fin 2, the motor...
Embodiment 2
[0039] Such as Figure 5 to Figure 8 As shown, the phase change heat dissipation motor casing described in this embodiment is similar to the phase change heat dissipation motor casing described in Embodiment 1, the difference lies in:
[0040] The outer surface of the above-mentioned annular shell 1 is provided with several grooves 11 arranged at intervals in the circumferential direction. The fin body 21 is made of micro-channel aluminum flat tubes, and the micro-channel aluminum flat tubes are embedded in the grooves 11. A plurality of heat dissipation through holes 231 are arranged in the microchannel aluminum flat tube 23 , and both ends of the heat dissipation through holes 231 are sealed to form the vacuum phase change heat dissipation channel 22 . The heat dissipation through hole 231 of the micro-channel aluminum flat tube 23 can be sealed by a cold-press sealing process.
[0041] The casing of the phase-change heat-dissipating motor described in this embodiment uses ...
Embodiment 3
[0048] Such as Figure 9 As shown, this embodiment provides an air-cooled motor, including a housing assembly, a stator assembly 4, a rotor assembly 5 and a rotating shaft 6, the rotor assembly 5 is mounted on the rotating shaft 6, and the stator assembly 4 is nested Installed in the casing assembly, the rotor assembly 5 is sleeved in the stator assembly 4, wherein the stator assembly 4 includes a stator core 41 and a coil winding 42 wound on the stator core 41, It is characterized in that: the shell assembly includes a shell shell 10 , an upper end cover 71 and a lower end cover 72 , and the shell shell 10 is the phase-change cooling motor casing described in the first or second embodiment.
[0049] The air-cooled motor described in this embodiment, through the use of the phase change heat dissipation motor casing, the heat of the internal coil winding 42 and the stator core 41 of the motor is quickly transferred to the ends of the heat dissipation fins 2, which improves the ...
PUM
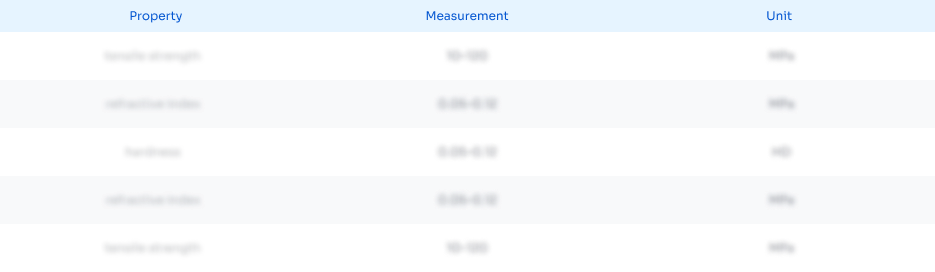
Abstract
Description
Claims
Application Information

- Generate Ideas
- Intellectual Property
- Life Sciences
- Materials
- Tech Scout
- Unparalleled Data Quality
- Higher Quality Content
- 60% Fewer Hallucinations
Browse by: Latest US Patents, China's latest patents, Technical Efficacy Thesaurus, Application Domain, Technology Topic, Popular Technical Reports.
© 2025 PatSnap. All rights reserved.Legal|Privacy policy|Modern Slavery Act Transparency Statement|Sitemap|About US| Contact US: help@patsnap.com