Manufacturing method of fuel cell assembly
A fuel cell, manufacturing method technology, applied in the direction of fuel cell components, fuel cells, final product manufacturing, etc.
- Summary
- Abstract
- Description
- Claims
- Application Information
AI Technical Summary
Problems solved by technology
Method used
Image
Examples
Embodiment Construction
[0036] Hereinafter, a preferred embodiment of the present invention will be described with reference to the drawings. figure 1 It is a cross-sectional view schematically showing a joining device 10 according to an embodiment of the present invention. exist figure 1 The main parts of the joining device 10 are shown in . figure 2 It is an enlarged cross-sectional view showing the configuration of the heat transfer member 20 and the heating member 30 of the present embodiment.
[0037] Such as figure 1 As shown, the bonding apparatus 10 of the present embodiment includes a placing jig 11 , a frame pressing member 12 , a bonded body pressing member 13 , a heat transfer member 20 , and a heating member 30 .
[0038] The placing jig 11 has the electrolyte membrane-electrode assembly 100 and the resin frame 150 placed on its upper surface. A concave portion 15 for placing the resin frame 150 is formed on the placing jig 11 . The electrolyte membrane-electrode assembly 100 is pl...
PUM
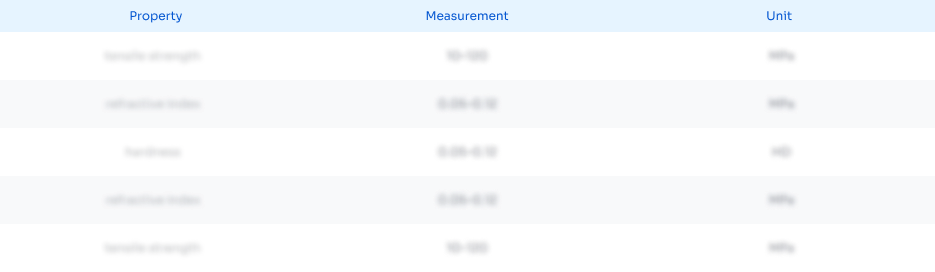
Abstract
Description
Claims
Application Information

- Generate Ideas
- Intellectual Property
- Life Sciences
- Materials
- Tech Scout
- Unparalleled Data Quality
- Higher Quality Content
- 60% Fewer Hallucinations
Browse by: Latest US Patents, China's latest patents, Technical Efficacy Thesaurus, Application Domain, Technology Topic, Popular Technical Reports.
© 2025 PatSnap. All rights reserved.Legal|Privacy policy|Modern Slavery Act Transparency Statement|Sitemap|About US| Contact US: help@patsnap.com