Heat insulation building composite material and preparation method thereof
A composite material and construction technology, applied in the field of building materials, can solve problems such as poor thermal insulation performance, low compressive strength, and heavy weight, and achieve the effects of small weight, good neutral salt spray resistance, and simple preparation methods
- Summary
- Abstract
- Description
- Claims
- Application Information
AI Technical Summary
Problems solved by technology
Method used
Examples
Embodiment 1
[0022] A thermal insulation building composite material, comprising the following components in parts by weight: 30 parts of construction waste powder, 6 parts of sodium mercaptobenzothiazole, 5 parts of methyl acetoacetate, 6 parts of disodium dihydrogen pyrophosphate, and 2 parts of water-based polyurethane 5 parts of barium metaphosphate, 2 parts of octadecatrienoic acid, 7 parts of illite, 8 parts of gangue, 5 parts of fluorocarbon alcohol, 0.5 part of glycyrrhetinic acid monoglucuronide, 0.5 part of lignin, superplasticizer 0.1 part.
[0023] A preparation method of thermal insulation building composite material, comprising the following steps:
[0024] (1) Add construction waste powder, illite, gangue, and barium metaphosphate into the mixer, and stir and mix for 10 minutes;
[0025] (2) Add the product obtained from the previous step into the reactor, continue to add sodium mercaptobenzothiazole, water-based polyurethane, lignin, and octadecatrienoic acid into the reac...
Embodiment 2
[0030] A thermal insulation building composite material, comprising the following components in parts by weight: 45 parts of construction waste powder, 8 parts of sodium mercaptobenzothiazole, 8 parts of methyl acetoacetate, 10 parts of disodium dihydrogen pyrophosphate, and 6 parts of water-based polyurethane 8 parts of barium metaphosphate, 5 parts of octadecatrienoic acid, 16 parts of illite, 15 parts of gangue, 8 parts of fluorocarbon alcohol, 1 part of glycyrrhetinic acid monoglucuronide, 1 part of lignin, superplasticizer 1 serving.
[0031] A preparation method of thermal insulation building composite material, comprising the following steps:
[0032] (1) Add construction waste powder, illite, gangue, and barium metaphosphate into the mixer, and stir and mix for 25 minutes;
[0033] (2) Add the product obtained from the previous step into the reactor, continue to add sodium mercaptobenzothiazole, water-based polyurethane, lignin, and octadecatrienoic acid into the reac...
Embodiment 3
[0038] A thermal insulation building composite material, comprising the following components in parts by weight: 38 parts of construction waste powder, 7 parts of sodium mercaptobenzothiazole, 7 parts of methyl acetoacetate, 9 parts of disodium dihydrogen pyrophosphate, and 5 parts of water-based polyurethane 7 parts of barium metaphosphate, 4 parts of octadecatrienoic acid, 13 parts of illite, 11 parts of gangue, 6 parts of fluorocarbon alcohol, 0.7 part of glycyrrhetinic acid monoglucuronide, 0.6 part of lignin, superplasticizer 0.3 parts.
[0039] A preparation method of thermal insulation building composite material, comprising the following steps:
[0040] (1) Add construction waste powder, illite, gangue, and barium metaphosphate into the mixer, and stir and mix for 20 minutes.
[0041] (2) Add the resultant from the previous step into the reaction kettle, continue to add sodium mercaptobenzothiazole, water-based polyurethane, lignin, and octadecatrienoic acid into the ...
PUM
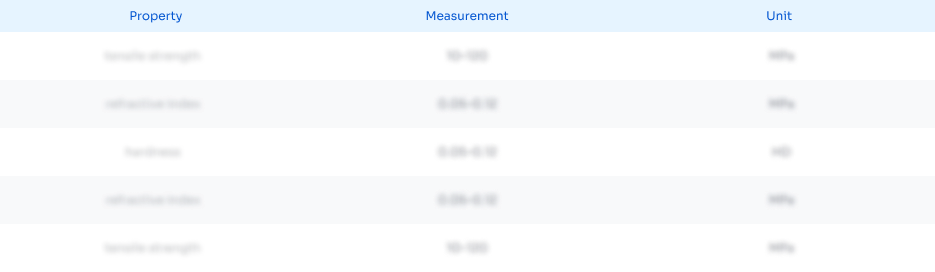
Abstract
Description
Claims
Application Information

- Generate Ideas
- Intellectual Property
- Life Sciences
- Materials
- Tech Scout
- Unparalleled Data Quality
- Higher Quality Content
- 60% Fewer Hallucinations
Browse by: Latest US Patents, China's latest patents, Technical Efficacy Thesaurus, Application Domain, Technology Topic, Popular Technical Reports.
© 2025 PatSnap. All rights reserved.Legal|Privacy policy|Modern Slavery Act Transparency Statement|Sitemap|About US| Contact US: help@patsnap.com