Low-energy-consumption environmentally-friendly magnetized calcination tailing cooling processing system
A magnetization roasting and processing system technology, which is applied in the field of low energy consumption and environment-friendly magnetization roasting tailings cooling and processing system, can solve the problems of liquid water mixed with heavy metals, waste of water resources, dehydration difficulties, etc., and achieves the degree of avoiding secondary oxidation and material cooling. uniform effect
- Summary
- Abstract
- Description
- Claims
- Application Information
AI Technical Summary
Problems solved by technology
Method used
Image
Examples
Embodiment Construction
[0023] Such as figure 1 Shown is a preferred embodiment of the present invention.
[0024] A low energy consumption and environment-friendly magnetized roasting tailings cooling treatment system, including a closed tailings cooling tank 1, the closed tailings cooling tank 1 is placed vertically, the upper part is provided with a material inlet 2, and the lower part is provided with a material outlet 3, and the tank is vertically installed with The water circulation spiral conveying pipeline 4; the water circulation spiral conveying pipeline 4 includes a water circulation spiral cavity 41 and a material spiral slideway 42, the material spiral slideway 42 is located on the upper surface of the water circulation spiral cavity 41, and spirals downward with the water circulation spiral cavity 41; The water circulation spiral channel 41 includes a water inlet 411 and a water outlet 412 .
[0025] The larger the orthographic area of the top surface of the material spiral slideway ...
PUM
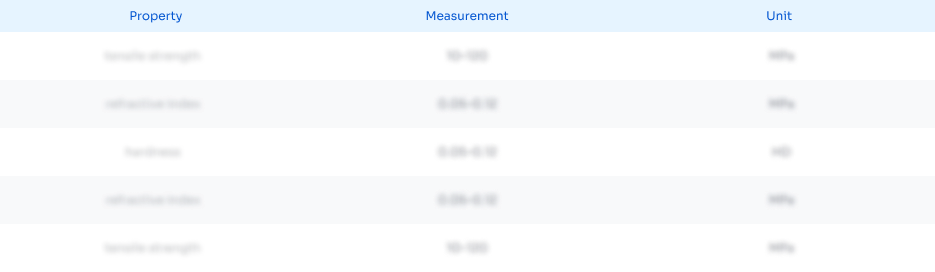
Abstract
Description
Claims
Application Information

- R&D
- Intellectual Property
- Life Sciences
- Materials
- Tech Scout
- Unparalleled Data Quality
- Higher Quality Content
- 60% Fewer Hallucinations
Browse by: Latest US Patents, China's latest patents, Technical Efficacy Thesaurus, Application Domain, Technology Topic, Popular Technical Reports.
© 2025 PatSnap. All rights reserved.Legal|Privacy policy|Modern Slavery Act Transparency Statement|Sitemap|About US| Contact US: help@patsnap.com