A metal bonded diamond grinding wheel
A diamond grinding wheel and metal bond technology, which is applied in metal processing equipment, manufacturing tools, abrasives, etc., can solve the problems of metal bond abrasive tool limitation, influence of workpiece surface quality, and easy burn on workpiece surface, so as to reduce the number of abrasive tools. Consume, improve bonding performance, increase the effect of self-sharpening
- Summary
- Abstract
- Description
- Claims
- Application Information
AI Technical Summary
Problems solved by technology
Method used
Examples
Embodiment 1
[0019] a. Moisten the diamond with liquid paraffin, add metal powder, copper-cerium alloy, TS-1 titanium-silicon molecular sieve, mix in a high-energy mixer for 20 hours, and fully mix; each raw material is respectively 46% Fe, 30% by weight %Cu, 5%Sn, 6%Cu-Ce, 2%Ni, 3%TS-1 titanium-silicon molecular sieve, 1% pore forming agent, 7% diamond composite abrasive grains; the TS-1 titanium-silicon molecular sieve is as follows Methods: Immerse 200-300nm TS-1 titanium-silicon molecular sieve in 5% cerium nitrate solution in acetone for 5 hours, filter, and slowly heat up and dry at a drying speed of 20°C / h, rising to 600°C and keeping warm 1h;
[0020] b. Vacuum hot pressing process is adopted, the sintering temperature is 620°C, the sintering pressure is 23 MPa, and the holding time is 12 minutes.
Embodiment 2
[0022] a. Wet the diamond with liquid paraffin, add metal powder, copper-cerium alloy, TS-1 titanium-silicon molecular sieve, mix in a high-energy mixer for 20 hours, and mix well; the raw materials are respectively 45.49% Fe, 34.55 % by weight %Cu, 6.83%Sn, 1.89%Cu-Ce, 1.41%Ni, 3%TS-1 titanium-silicon molecular sieve, 1.12% pore forming agent, 5.71% diamond composite abrasive grains; the TS-1 titanium-silicon molecular sieve is as follows Methods: Immerse 200-300nm TS-1 titanium-silicon molecular sieve into 10% cerium nitrate solution in acetone for 2 hours, filter, slowly heat up and dry at a drying speed of 20°C / h, rise to 600°C, and keep warm 1h;
[0023] b. The vacuum hot pressing process is adopted, the sintering temperature is 640°C, the sintering pressure is 23 MPa, and the holding time is 10 minutes.
Embodiment 3
[0025] a. Wet the diamond with liquid paraffin, add metal powder, copper-cerium alloy, TS-1 titanium-silicon molecular sieve, mix in a high-energy mixer for 20 hours, and mix well; each raw material is 12.39% by weight respectively Granules, 41.27% Fe, 33.93% Cu, 6.34% Sn, 1.76% Cu-Ce, 1.31% Ni, 3% TS-1 titanium-silicon molecular sieve; the TS-1 titanium-silicon molecular sieve is obtained through the following method: 200-300nm TS-1 titanium-silicon molecular sieves were immersed in 8% cerium nitrate solution in acetone for 4 hours, filtered, and then slowly heated and dried at a drying speed of 20°C / h, raised to 600°C, and kept for 1 hour;
[0026] b. Vacuum hot pressing process is adopted, the sintering temperature is 650°C, the sintering pressure is 24MPa and the holding time is 8min.
PUM
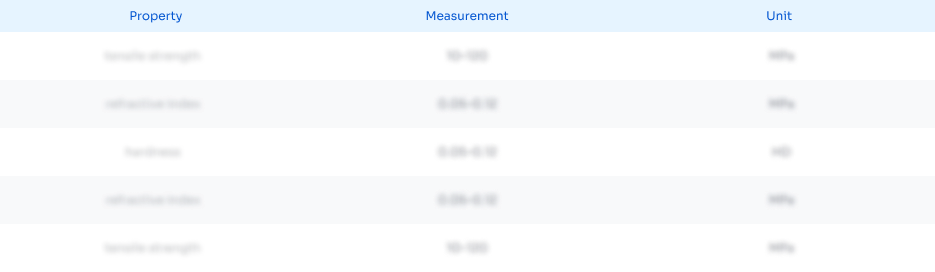
Abstract
Description
Claims
Application Information

- R&D
- Intellectual Property
- Life Sciences
- Materials
- Tech Scout
- Unparalleled Data Quality
- Higher Quality Content
- 60% Fewer Hallucinations
Browse by: Latest US Patents, China's latest patents, Technical Efficacy Thesaurus, Application Domain, Technology Topic, Popular Technical Reports.
© 2025 PatSnap. All rights reserved.Legal|Privacy policy|Modern Slavery Act Transparency Statement|Sitemap|About US| Contact US: help@patsnap.com