Canned spray type welding anti-splashing agent and preparation method thereof
An anti-splash agent and canned technology, which is applied in welding equipment, welding medium, welding/cutting medium/material, etc., can solve the problems of local air pollution, pollution, waste of consumption, etc., to reduce arc discharge and metal spatter , The effect of simple production process
- Summary
- Abstract
- Description
- Claims
- Application Information
AI Technical Summary
Problems solved by technology
Method used
Examples
Embodiment 1
[0048] (1) 40Kg of petroleum ether, 20Kg of ethyl acetate and 35Kg of ethanol with a volume fraction of 95% were prepared as a mixed solvent and added to the reaction kettle, and the temperature was raised to 55°C under reflux;
[0049] (2) Add 2Kg alcohol-soluble polyamide, 2Kg rosin glyceride, 2Kg terpene phenol resin and 2Kg C5 petroleum resin to the mixed solvent in sequence and fully dissolve to obtain a uniform and transparent sol water-like substance;
[0050](3) Add 1Kg 4000-5000 mesh fumed silica under reflux shearing and stirring state, add 2Kg 100-200nm nano-alumina and 1Kg zinc chloride after stirring for 15 minutes, add 3Kg 2000-3000 mesh golden red after stirring for 15 minutes Stone powder, continue to stir and mix evenly to obtain a uniform bright white creamy flowable slurry;
[0051] (4) Stir the slurry to cool down to room temperature, then add 0.03% of fluorescent green to the total mass of the slurry, adjust the solid content of the slurry to 12% according...
Embodiment 2
[0054] (1) Prepare a mixed solvent with 50Kg of petroleum ether, 15Kg of ethyl acetate and 20Kg of ethanol with a volume fraction of 95%, and heat up to 45°C under reflux;
[0055] (2) Add 1Kg alcohol-soluble polyamide, 1Kg rosin glyceride, 1Kg terpene phenol resin and 1Kg C5 petroleum resin to the mixed solvent in sequence and fully dissolve to obtain a uniform and transparent sol water-like substance;
[0056] (3) Add 1Kg 4000-5000 mesh fumed silica under reflux shear stirring state, stir for 15 minutes, add 1Kg 100-200nm nano-alumina and 1Kg zinc chloride, stir for 15 minutes, add 2Kg 2000-3000 mesh golden red Stone powder, continue to stir and mix evenly to obtain a uniform bright white creamy flowable slurry;
[0057] (4) Stir the slurry to cool down to room temperature, then add 0.01% of fluorescent green to the total mass of the slurry, adjust the solid content of the slurry to 5% according to different welding conditions, and finally obtain a white and micro-green milk...
Embodiment 3
[0060] (1) Mix 60Kg of petroleum ether, 20Kg of ethyl acetate and 40Kg of isopropanol into a mixed solvent, and heat up to 50°C under reflux;
[0061] (2) Add 3Kg alcohol-soluble polyamide, 2Kg rosin glyceride, 2Kg terpene phenol resin and 2Kg C5 petroleum resin to the mixed solvent in sequence and fully dissolve to obtain a uniform and transparent sol water-like substance;
[0062] (3) Add 2Kg 4000-5000 mesh fumed silica under reflux shearing and stirring state, add 2Kg 100-200nm nano-alumina and 2Kg zinc chloride after stirring for 15 minutes, add 3Kg 2000-3000 mesh golden red after stirring for 15 minutes Stone powder, continue to stir and mix evenly to obtain a uniform bright white creamy flowable slurry;
[0063] (4) Stir the slurry to cool down to room temperature, then add 0.05% of fluorescent green to the total mass of the slurry, adjust the solid content of the slurry to 15% according to different welding conditions, and finally obtain a white and micro-green milky sm...
PUM
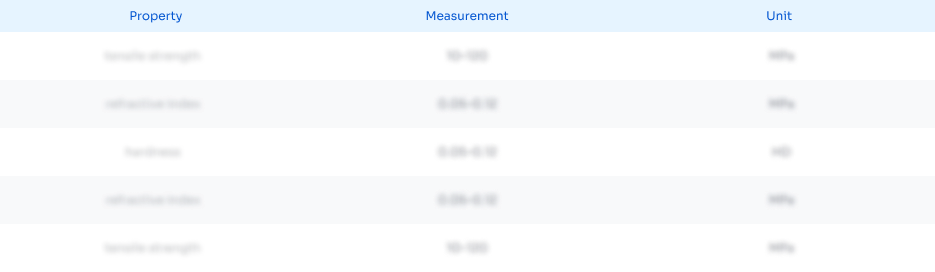
Abstract
Description
Claims
Application Information

- R&D
- Intellectual Property
- Life Sciences
- Materials
- Tech Scout
- Unparalleled Data Quality
- Higher Quality Content
- 60% Fewer Hallucinations
Browse by: Latest US Patents, China's latest patents, Technical Efficacy Thesaurus, Application Domain, Technology Topic, Popular Technical Reports.
© 2025 PatSnap. All rights reserved.Legal|Privacy policy|Modern Slavery Act Transparency Statement|Sitemap|About US| Contact US: help@patsnap.com