A urea granulation process without adding formaldehyde
A urea granulation technology that does not need to be added. It is applied in the direction of urea compound fertilizer, separation of dispersed particles, liquid into beads and granulation, etc. It can solve the problems of secondary pollution hazards and loss, and achieve environmental protection and safety in the production process. Production cost Low, effective storage and application
- Summary
- Abstract
- Description
- Claims
- Application Information
AI Technical Summary
Problems solved by technology
Method used
Image
Examples
Embodiment 1
[0040] This embodiment relates to the technological process of the method of the present invention (its flow chart sees figure 1 ),details as follows:
[0041] The urea solution is sent to the granulator 102 through the granulation feed pump 101 for granulation. The granulator is a fluidized bed granulation equipment, including a fluidizing air fan 103 and an atomizing air fan 104 . After the large-grain urea produced by the granulator passes through the drying and cooling process of the fluidized bed dryer 105, the particle size is sieved through the urea sieve 106. or The large granular urea product becomes a qualified formaldehyde-free large granular urea product after being cooled by the final product cooler 107.
[0042] In addition, the air containing urea dust discharged from the granulator enters the dust scrubber 109, and after being wet-washed with water, the tail gas is discharged into the atmosphere. General exhaust gas contains urea dust 20mg / m 3 . The ai...
Embodiment 2
[0044] This embodiment relates to a preparation process of urea granules, comprising the following steps:
[0045] 1) urea solution with a mass concentration of 75% is used as a raw material, and is fed into a granulator at a pressure of 0.6 MPa and a temperature of 135° C., and is granulated by an atomized fluidized bed granulation process;
[0046] Control the temperature of the fluidized bed in the granulator to 100°C, and the outlet product temperature to 100°C;
[0047] 2) After the granulation is completed, the urea granules are dried at 60°C;
[0048] 3) After the drying is completed, the urea granules are sieved, and the sieved particle size is or The product is finally cooled to below 50°C to obtain formaldehyde-free large particle urea.
Embodiment 3
[0050] This embodiment relates to a preparation process of urea granules, comprising the following steps:
[0051] 1) urea solution with a mass concentration of 99% is used as a raw material, and is fed into a granulator at a pressure of 0.2 MPa and a temperature of 135° C., and is granulated by an atomized fluidized bed granulation process;
[0052] Control the temperature of the fluidized bed in the granulator to 115°C, and the outlet product temperature to 110°C;
[0053] 2) After the granulation is completed, the urea granules are dried at 100°C;
[0054] 3) After the drying is completed, the urea granules are sieved, and the sieved particle size is or The product is finally cooled to below 50°C to obtain formaldehyde-free large particle urea.
PUM
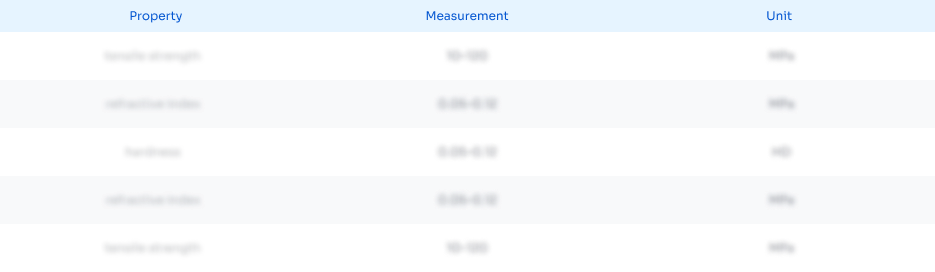
Abstract
Description
Claims
Application Information

- R&D
- Intellectual Property
- Life Sciences
- Materials
- Tech Scout
- Unparalleled Data Quality
- Higher Quality Content
- 60% Fewer Hallucinations
Browse by: Latest US Patents, China's latest patents, Technical Efficacy Thesaurus, Application Domain, Technology Topic, Popular Technical Reports.
© 2025 PatSnap. All rights reserved.Legal|Privacy policy|Modern Slavery Act Transparency Statement|Sitemap|About US| Contact US: help@patsnap.com