Ship and naval vessel wall surface wall-climbing cleaning robot
A technology for cleaning robots and cleaning mechanisms, which is applied to grinding frames, grinding machine parts, grinding machines, etc. It can solve the problems of lack of self-adaptive structural design, inability to adapt to large curvature hull surfaces, and unreliable adsorption.
- Summary
- Abstract
- Description
- Claims
- Application Information
AI Technical Summary
Problems solved by technology
Method used
Image
Examples
Embodiment 1
[0031] Such as Figure 1-Figure 2 A wall-climbing cleaning robot for ships and warships shown includes a vehicle frame 1 on which a walking adaptive mechanism 2 , a cleaning mechanism 3 and a thrust adsorption mechanism 4 are installed.
[0032] Such as image 3 with Figure 4 As shown, the walking adaptive mechanism 2 includes a crawler belt 5, and the crawler belt 5 is set on the driving wheel 6 and the tensioning wheel 7; the tensioning wheel 7 is connected with a telescopic adjustment mechanism 8, and the telescopic adjustment mechanism 8 is a hydraulic cylinder or other telescopic device. Such as cylinders, etc. An adaptive mechanism is installed between the driving wheel 6 and the tensioning wheel 7; the adaptive mechanism includes a spring 9, one end of the spring 9 is connected to the vehicle frame 1, and the other end is connected to the upper support plate 10, and the support plate 10 is connected to the vehicle frame 1 shaft through the rotating shaft 14. Connect...
PUM
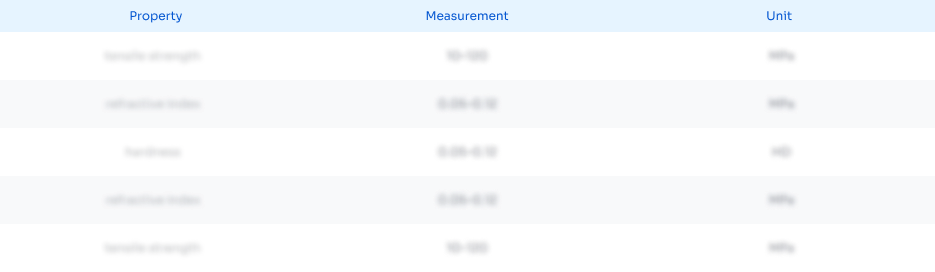
Abstract
Description
Claims
Application Information

- Generate Ideas
- Intellectual Property
- Life Sciences
- Materials
- Tech Scout
- Unparalleled Data Quality
- Higher Quality Content
- 60% Fewer Hallucinations
Browse by: Latest US Patents, China's latest patents, Technical Efficacy Thesaurus, Application Domain, Technology Topic, Popular Technical Reports.
© 2025 PatSnap. All rights reserved.Legal|Privacy policy|Modern Slavery Act Transparency Statement|Sitemap|About US| Contact US: help@patsnap.com