A kind of chloropropene oxidation method
A technology of chloropropene and oxidant, which is applied in chemical instruments and methods, organic chemistry, molecular sieve catalysts, etc., can solve the problems of increasing device operating costs, equipment corrosion, reactor shutdown, etc. The effect of reducing the regeneration frequency
- Summary
- Abstract
- Description
- Claims
- Application Information
AI Technical Summary
Problems solved by technology
Method used
Image
Examples
Embodiment approach
[0068] According to the method of the present invention, the amounts (mass) of the titanium-silicon molecular sieves loaded in the first to nth catalyst beds may be the same or different. According to one implementation, when m is any integer in the interval [2, n], W m-1 / W m 0.1-20, W m-1 / W m Preferably it is 0.5 or more, More preferably, it is 1 or more, More preferably, it is 2 or more. Here, W m-1 is the quality of the catalyst packed in the upstream catalyst bed in any pair of adjacent catalyst beds from the first catalyst bed to the last nth catalyst bed, W m is the mass of the catalyst loaded in the downstream catalyst bed in any pair of adjacent catalyst beds from the first catalyst bed to the nth catalyst bed. W m-1 / W m Preferably it is 15 or less, and more preferably 10 or less. More preferably, W m-1 / W m for 2-8. W m-1 and W m It is determined by the content of the titanium-silicon molecular sieve in the shaped titanium-silicon molecular sieve. In ...
Embodiment 1
[0097] The catalyst used in this example is titanium-silicon molecular sieve TS-1, prepared according to the method described in Zeolites, 1992, Vol.12, pages 943-950, and the specific method is as follows.
[0098] At room temperature (20°C), mix 22.5g tetraethyl orthosilicate with 7.0g tetrapropylammonium hydroxide as a template, add 59.8g distilled water, stir and mix, then hydrolyze at normal pressure and 60°C for 1.0h , to obtain a hydrolysis solution of tetraethyl orthosilicate. Under vigorous stirring, a solution consisting of 1.1 g of tetrabutyl titanate and 5.0 g of anhydrous isopropanol was slowly added to the hydrolysis solution, and the resulting mixture was stirred at 75° C. for 3 h to obtain a clear transparent colloid. The colloid was placed in a sealed stainless steel reaction kettle, and kept at a constant temperature of 170° C. for 36 hours to obtain a mixture of crystallized products. The obtained mixture was filtered, the collected solid matter was washed ...
Embodiment 2
[0104] Propylene chloride was oxidized by the same method as in Example 1, except that the titanium-silicon molecular sieve TS-1 used was prepared by the following method.
[0105] Dissolve tetrabutyl titanate in the alkali source template agent tetrapropyl ammonium hydroxide aqueous solution first, then add silica gel (purchased from Qingdao Silica Gel Factory) to obtain a dispersion. In the dispersion, silicon source: titanium source: alkali source Template agent: water molar ratio is 100:4:12:400, silicon source is SiO 2 In terms of titanium source as TiO 2 In terms of alkali source template agent in N. Seal the above dispersion in the beaker with a parafilm and let it stand at room temperature (25°C, the same below) for 24h, then stir at 35°C for 2h with magnetic stirring to redisperse it. Transfer the re-dispersed dispersion liquid to a sealed reaction kettle, undergo the first stage of crystallization at 140°C for 6h, then cool the mixture down to 30°C and experience t...
PUM
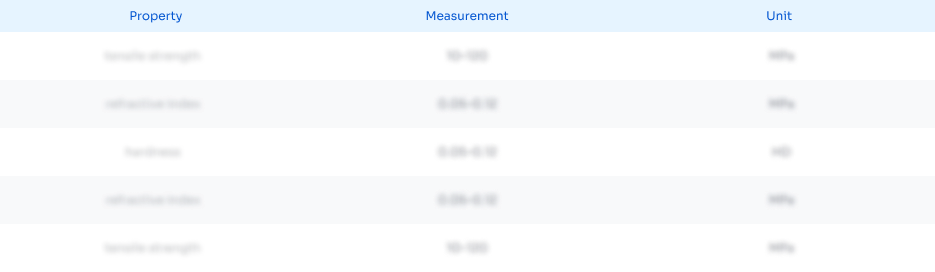
Abstract
Description
Claims
Application Information

- Generate Ideas
- Intellectual Property
- Life Sciences
- Materials
- Tech Scout
- Unparalleled Data Quality
- Higher Quality Content
- 60% Fewer Hallucinations
Browse by: Latest US Patents, China's latest patents, Technical Efficacy Thesaurus, Application Domain, Technology Topic, Popular Technical Reports.
© 2025 PatSnap. All rights reserved.Legal|Privacy policy|Modern Slavery Act Transparency Statement|Sitemap|About US| Contact US: help@patsnap.com