Friction wedge type automatic clamp for cylindrical grinding and application method thereof
A friction wedge, automatic technology, applied in the direction of grinding workpiece support, etc., can solve the problems of low degree of automation, eccentric rotation of the workpiece, affecting machining accuracy, etc., to achieve automatic clamping, ensure grinding accuracy, and improve clamping accuracy Effect
- Summary
- Abstract
- Description
- Claims
- Application Information
AI Technical Summary
Problems solved by technology
Method used
Image
Examples
Embodiment Construction
[0019] Such as figure 1 , 2 As shown, the friction wedge type external grinding automatic fixture includes connecting flange 1, screw M6X252, left end cover 3, screw M5X254, head frame top 5, spacer 6, bearing positioning sleeve 7, machine tool head frame pulley 8, positioning Flange 9, intermediate sleeve 10, outer cone spring 11, inner cone spring 12, spring positioning piece 13, complete needle roller bearing 14, hex nut 15, bearing positioning ring 16, stop ring 17, spline inner sleeve 18 , support ring 19, positioning sleeve 20, wedge ring 21, dial ring 22, return spring 23, spring sleeve 24, dial pin 25, dial nut 26, wedge 27, spacer 28, support ring positioning sleeve 29, Needle bearing 30, screw M6X5031, screw M6X3032, sleeve stop ring 33, right end cover 34, top stop ring 35, needle bearing 36 and spacer 37;
[0020] The connecting flange 1 and the positioning flange 9 are fastened to the gear rotor and stator of the pulley 8 of the machine head frame through screws...
PUM
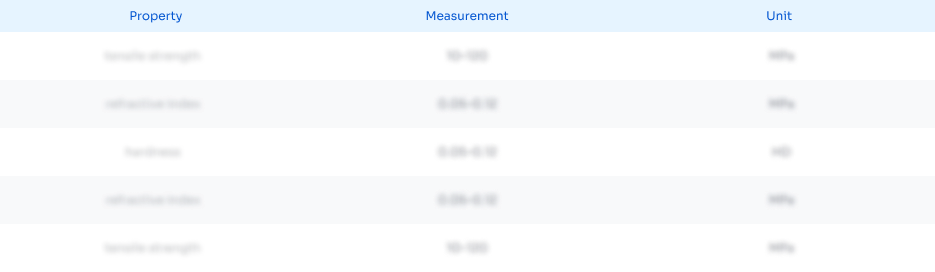
Abstract
Description
Claims
Application Information

- R&D
- Intellectual Property
- Life Sciences
- Materials
- Tech Scout
- Unparalleled Data Quality
- Higher Quality Content
- 60% Fewer Hallucinations
Browse by: Latest US Patents, China's latest patents, Technical Efficacy Thesaurus, Application Domain, Technology Topic, Popular Technical Reports.
© 2025 PatSnap. All rights reserved.Legal|Privacy policy|Modern Slavery Act Transparency Statement|Sitemap|About US| Contact US: help@patsnap.com