Automatic drilling and milling system and method and drilling and milling production line
An automatic drilling, drilling and milling technology, applied in the direction of automatic control devices, manufacturing tools, other manufacturing equipment/tools, etc., can solve problems such as inability to complete waist hole milling, inability to adapt to workpiece wall thickness differences, and processing errors
- Summary
- Abstract
- Description
- Claims
- Application Information
AI Technical Summary
Problems solved by technology
Method used
Image
Examples
Embodiment 1
[0109] figure 1 It is a schematic diagram of the module structure of the automatic drilling and milling system in the embodiment of the application; as figure 1 As shown, an automatic drilling and milling system in this embodiment can be applied to operations such as drilling / milling on workpieces to be processed (such as aluminum structural parts, etc.) fixed on a processing table, and the system may include:
[0110] A robot (i.e. an industrial robot) can be fixedly arranged at a position close to the above-mentioned processing table, so that the robot can be used to perform operations such as drilling / milling on the workpiece to be processed;
[0111] The drilling and milling module is connected with the above-mentioned robot (that is, mechanically connected and fixed on the above-mentioned robot), which can make the robot drive the drilling and milling module to perform operations such as drilling / milling on the workpiece to be processed;
[0112] The scanning detection m...
Embodiment 2
[0124] The application also provides a drilling and milling production line, comprising:
[0125] Material loading sub-production line, at least one drilling and milling sub-production line and deburring processing sub-production line, and the automatic drilling and milling system in the first embodiment of the drilling and milling sub-production line;
[0126] Specifically, after the feeding sub-generation line fixes the workpiece to be processed on the processing table, the drilling and milling sub-generation line performs drilling / milling operations on the workpiece to be processed fixed on the processing table, and the deburring processing sub-generation line removes the workpiece after drilling and milling. After the sub-system performs the drilling / milling operation, the workpiece to be processed is deburred.
Embodiment 3
[0128] image 3 It is a schematic flow chart of robot position / posture online compensation in the automatic drilling and milling method in the embodiment of the present application; Figure 4 It is a schematic flow chart of real-time adjustment of cutting parameters in the automatic drilling and milling method in the embodiment of the present application; Figure 1~4 As shown, the present application also provides an automatic drilling and milling method, which can be based on the above-mentioned embodiment 1 and / or embodiment 2, including:
[0129] Fix the workpiece to be processed on the processing table;
[0130] Use the robot to drive the drilling and milling module to perform drilling / milling operations on the workpiece to be processed;
[0131] The scanning detection module obtains the processing position information and actual cutting parameter information of the drilling / milling operation;
[0132] The online compensation processing module corrects the drilling / mill...
PUM
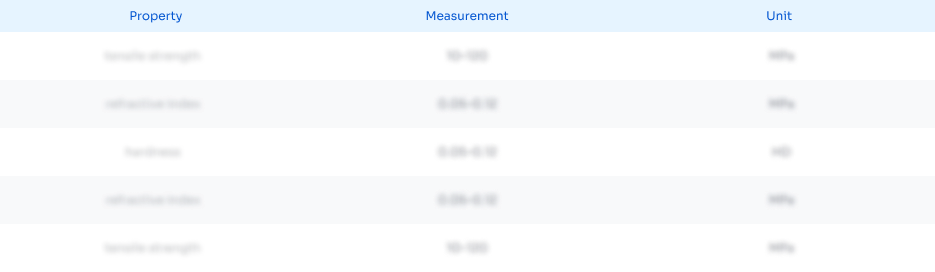
Abstract
Description
Claims
Application Information

- R&D
- Intellectual Property
- Life Sciences
- Materials
- Tech Scout
- Unparalleled Data Quality
- Higher Quality Content
- 60% Fewer Hallucinations
Browse by: Latest US Patents, China's latest patents, Technical Efficacy Thesaurus, Application Domain, Technology Topic, Popular Technical Reports.
© 2025 PatSnap. All rights reserved.Legal|Privacy policy|Modern Slavery Act Transparency Statement|Sitemap|About US| Contact US: help@patsnap.com