Production method of flax/cotton blended yarns
A production method, cotton blending technology, applied in the direction of yarn, textiles and papermaking, etc., can solve the problems of uneven fiber distribution and poor performance, and achieve high strength, meet functional requirements, and small CV value of single strength.
- Summary
- Abstract
- Description
- Claims
- Application Information
AI Technical Summary
Problems solved by technology
Method used
Examples
Embodiment 1
[0011] The production method of hemp / cotton blended yarn of the present invention, comprises the steps:
[0012] 1) Pretreatment of hemp fiber: first rub and comb the flax fiber, then spray softener to soften it, and then seal it for 24 hours to soften the fiber and pack it to obtain hemp fiber with improved performance;
[0013] 2) After the hemp fiber and cotton fiber are mixed, they are sequentially passed through the disc plucking machine, cotton blending machine, porcupine opener, multi-compartment blending machine, card roller opener, vibrating cotton feeder, and single beater. Processing of coiling machine, carding machine, three-way draw frame, roving frame, siro spinning frame and winding machine to obtain hemp / cotton blended yarn.
[0014] The weight ratio of the hemp fiber and cotton fiber is 1:3.
Embodiment 2
[0016] The production method of hemp / cotton blended yarn of the present invention, comprises the steps:
[0017] 1) Pretreatment of hemp fiber: first rub and comb the flax fiber, then spray softener to soften it, and then seal it for 24 hours to soften the fiber and pack it to obtain hemp fiber with improved performance;
[0018] 2) After the hemp fiber and cotton fiber are mixed, they are sequentially passed through the disc plucking machine, cotton blending machine, porcupine opener, multi-compartment blending machine, card roller opener, vibrating cotton feeder, and single beater. Processing of coiling machine, carding machine, three-way draw frame, roving frame, siro spinning frame and winding machine to obtain hemp / cotton blended yarn.
[0019] The weight ratio of the hemp fiber to the cotton fiber is 1:5.
Embodiment 3
[0021] The production method of hemp / cotton blended yarn of the present invention, comprises the steps:
[0022] 1) Pretreatment of hemp fiber: first rub and comb the flax fiber, then spray softener to soften it, and then seal it for 24 hours to soften the fiber and pack it to obtain hemp fiber with improved performance;
[0023] 2) After the hemp fiber and cotton fiber are mixed, they are sequentially passed through the disc plucking machine, cotton blending machine, porcupine opener, multi-compartment blending machine, card roller opener, vibrating cotton feeder, and single beater. Processing of coiling machine, carding machine, three-way draw frame, roving frame, siro spinning frame and winding machine to obtain hemp / cotton blended yarn.
[0024] The weight ratio of the hemp fiber to the cotton fiber is 1:4.
PUM
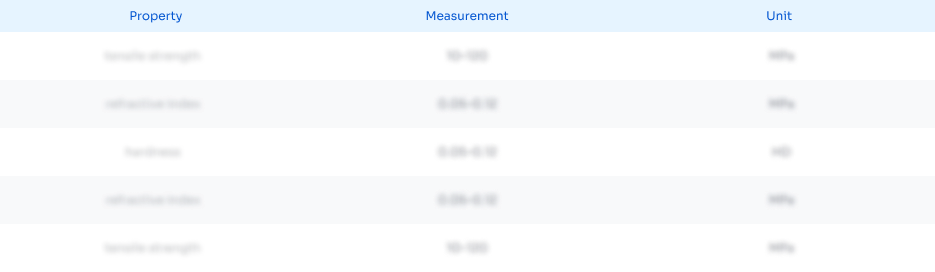
Abstract
Description
Claims
Application Information

- Generate Ideas
- Intellectual Property
- Life Sciences
- Materials
- Tech Scout
- Unparalleled Data Quality
- Higher Quality Content
- 60% Fewer Hallucinations
Browse by: Latest US Patents, China's latest patents, Technical Efficacy Thesaurus, Application Domain, Technology Topic, Popular Technical Reports.
© 2025 PatSnap. All rights reserved.Legal|Privacy policy|Modern Slavery Act Transparency Statement|Sitemap|About US| Contact US: help@patsnap.com