Rotary machine vibration signal fault identification method
A technology of rotating machinery and vibration signals, which is applied in the testing of mechanical components, mechanical bearings, and testing of machine/structural components. It can solve the problem of limited number of fault samples, difficulty in obtaining fault samples, and failure to consider the frequency classification of mechanical vibration signals, etc. problems, to achieve accurate results
- Summary
- Abstract
- Description
- Claims
- Application Information
AI Technical Summary
Problems solved by technology
Method used
Image
Examples
Embodiment 1
[0012] Due to the influence of factors such as rotational speed, load and impact caused by faults, the vibration signals of mechanical equipment often show strong non-stationarity. For the non-stationary signal of the vibration signal, it is not enough to only know the global characteristics of the signal in the time domain or frequency domain, and it is also hoped to obtain the signal spectrum of the vibration signal changing with time. Time-frequency analysis technology is to transform the signal into two-dimensional time-frequency domain for analysis, and it is an effective means to analyze non-stationary signals. The fault diagnosis method based on the time-domain characteristics of different frequency bands after the vibration signal is decomposed does not consider the frequency-domain characteristics of the vibration signal. The fault diagnosis method of mechanical vibration signal based on time-frequency domain features can use singular value decomposition method for fe...
Embodiment 2
[0016] Signal noise reduction for mechanical vibration signals. The signal noise reduction method based on empirical mode decomposition has a better noise reduction effect on low-frequency components. The reason is that the filter can smooth the signal, and the low-frequency components are relatively smooth. , which can better preserve the characteristics of low-frequency components; while the threshold-based noise reduction method has a better noise reduction effect on high-frequency components, and it can better maintain the high-frequency characteristics of high-frequency components. In order to make the noise reduction method based on the noise reduction method based on the low frequency part and the high frequency part of the signal can achieve better noise reduction effect, it is considered to combine the method based on the threshold value noise reduction method with the noise reduction method based on the first few components obtained by decomposition (higher frequencie...
PUM
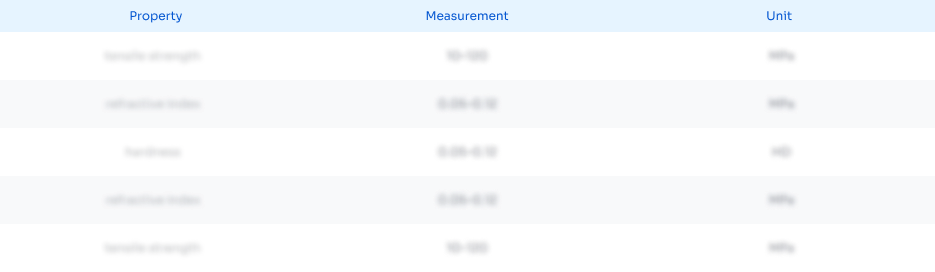
Abstract
Description
Claims
Application Information

- R&D
- Intellectual Property
- Life Sciences
- Materials
- Tech Scout
- Unparalleled Data Quality
- Higher Quality Content
- 60% Fewer Hallucinations
Browse by: Latest US Patents, China's latest patents, Technical Efficacy Thesaurus, Application Domain, Technology Topic, Popular Technical Reports.
© 2025 PatSnap. All rights reserved.Legal|Privacy policy|Modern Slavery Act Transparency Statement|Sitemap|About US| Contact US: help@patsnap.com