Solution heat treatment method for manufacturing metallic components of a turbo machine
A technology of solution heat treatment and metal parts, which is applied in the direction of engine components, blade support components, furnace components, etc., can solve the problems of inability to achieve material properties, conflicts, short retention time of thick sections, etc., and achieve good solution heat treatment Process, homogeneous temperature distribution, effect of reduced process variation
- Summary
- Abstract
- Description
- Claims
- Application Information
AI Technical Summary
Problems solved by technology
Method used
Image
Examples
Embodiment Construction
[0037] In a preferred embodiment, the invention is based on the combination of conditioning of complex components, preferably made of SX / DX-nickel-based or cobalt-based superalloys, to be processed in the application of inert gas flow Simultaneously a solution heat treatment (by wrapping a part of the part to control the heat flux) is carried out in the furnace with a specific positioning and installation of the part in the furnace. Components made from conventionally cast (CC) nickel- or cobalt-based superalloys can also be processed by the disclosed method.
[0038] The solution heated component is preferably a gas turbine component with internal cooling channels, preferably a turbine blade with an airfoil section with low thermal inertia and a root section with high thermal inertia, with an airfoil with low thermal inertia sections and guide vanes for 2 or 1 platform sections with large thermal inertia, or thermal shields.
[0039] figure 1 A simplified sketch of such a c...
PUM
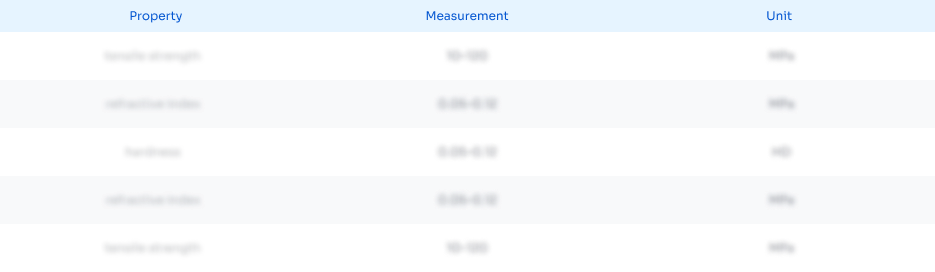
Abstract
Description
Claims
Application Information

- R&D
- Intellectual Property
- Life Sciences
- Materials
- Tech Scout
- Unparalleled Data Quality
- Higher Quality Content
- 60% Fewer Hallucinations
Browse by: Latest US Patents, China's latest patents, Technical Efficacy Thesaurus, Application Domain, Technology Topic, Popular Technical Reports.
© 2025 PatSnap. All rights reserved.Legal|Privacy policy|Modern Slavery Act Transparency Statement|Sitemap|About US| Contact US: help@patsnap.com