Emulsified cutting fluid
A cutting fluid and anti-oxidant technology, applied in the petroleum industry, lubricating composition, etc., can solve the problems of perishable, smelly, service life to be extended, etc., to achieve non-perishable, long service life, good anti-wear performance and lubrication performance effect
- Summary
- Abstract
- Description
- Claims
- Application Information
AI Technical Summary
Problems solved by technology
Method used
Examples
Embodiment approach
[0006] As an embodiment of the present invention, an emulsified cutting fluid includes the following raw materials in parts by weight: 20-40 parts of mineral oil, 4-12 parts of tall oil, 3-7 parts of extreme pressure additives, 0.1- 0.6 parts, 0.2-1.5 parts of copper alloy corrosion inhibitor, 0.1-1 part of antioxidant, 0.5-2 parts of defoamer, 0.5-1.5 parts of pour point depressant, and the balance is deionized water.
[0007] The method for preparing the above emulsified cutting fluid is: mix mineral oil, extreme pressure additives, and appropriate amount of deionized water at 60-80 degrees Celsius for 30-50 minutes, then add tall oil, rust inhibitor, copper alloy corrosion inhibitor , anti-oxidant, remaining deionized water, and stir and mix at 60-80 degrees Celsius for 30-50 minutes, finally add defoamer and pour point depressant, stir evenly, let it cool down, put it into a grinder and grind for 20-30 minutes , the above emulsified cutting fluid can be obtained.
[0008]...
Embodiment 1
[0010] An emulsified cutting fluid, comprising the following raw materials in parts by weight: 20 parts of kerosene, 4 parts of tall oil, 3 parts of chlorinated paraffin, 0.1 part of dodecenylsuccinic acid, 0.2 part of benzotriazole, di-tert-butyl 0.1 part of p-cresol, 0.5 part of defoamer, 0.5 part of polyalkylacrylate, and the balance is deionized water.
[0011] The method for preparing the above-mentioned emulsified cutting fluid is: mix kerosene, chlorinated paraffin, and appropriate amount of deionized water at 60-80 degrees Celsius for 30-50 minutes, then add tall oil, dodecenylsuccinic acid, benzo Triazole, di-tert-butyl p-cresol, and the remaining deionized water, and stirred and mixed at 60-80 degrees Celsius for 30-50 minutes, and finally added defoamer and polyalkyl acrylate, stirred evenly, and stood to cool. Put it into a grinder and grind it for 20-30 minutes to get the above emulsified cutting fluid. The maximum non-seize load value PB of the emulsified cuttin...
Embodiment 2
[0013] An emulsified cutting fluid, comprising the following raw materials in parts by weight: 20 parts of kerosene, 20 parts of diesel oil, 12 parts of tall oil, 3 parts of chlorinated paraffin, 4 parts of vulcanized lard, 0.3 parts of dodecenylsuccinic acid, petroleum 0.3 part of sulfonate, 0.5 part of benzotriazole, 1 part of sodium mercaptobenzothiazole, 0.5 part of di-tert-butyl p-cresol, 0.5 part of p-phenylenediamine, 2 parts of defoamer, polyalkyl acrylate 0.5 part, 1 part of polyisobutylene, and the balance is deionized water.
[0014] The method for preparing the above emulsified cutting fluid is: mix kerosene, diesel oil, chlorinated paraffin, vulcanized lard, and appropriate amount of deionized water at 60-80 degrees Celsius for 30-50 minutes, then add tall oil, petroleum sulfonate , dodecenylsuccinic acid, benzotriazole, sodium mercaptobenzothiazole, di-tert-butyl p-cresol, p-phenylenediamine, the remaining deionized water, and stir and mix at 60-80 degrees Celsiu...
PUM
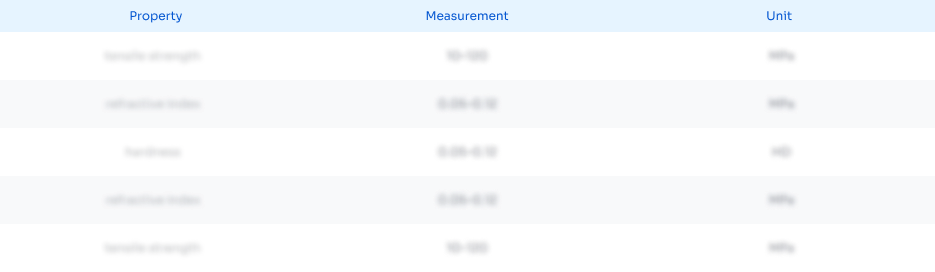
Abstract
Description
Claims
Application Information

- R&D
- Intellectual Property
- Life Sciences
- Materials
- Tech Scout
- Unparalleled Data Quality
- Higher Quality Content
- 60% Fewer Hallucinations
Browse by: Latest US Patents, China's latest patents, Technical Efficacy Thesaurus, Application Domain, Technology Topic, Popular Technical Reports.
© 2025 PatSnap. All rights reserved.Legal|Privacy policy|Modern Slavery Act Transparency Statement|Sitemap|About US| Contact US: help@patsnap.com