Method for preparing rubber filler by using inorganic salt for neutralizing alkali lignin
A technology for alkali lignin and rubber filler, which is applied in the field of preparing rubber filler by neutralizing alkali lignin with inorganic salts, can solve problems such as environmental pollution, waste of alkali lignin, etc., so as to solve the problem of environmental pollution, improve utilization, and reduce production cost Effect
- Summary
- Abstract
- Description
- Claims
- Application Information
AI Technical Summary
Problems solved by technology
Method used
Image
Examples
Embodiment 1
[0023] At room temperature, add 30 grams of alkali lignin, 19.5 grams of calcium-based montmorillonite, 7.8 grams of aluminum sulfate octadecahydrate and 120 grams of deionized water in a 500 ml ball mill jar, mix, the pH of the mixture is 7, and ball mill 3h, and finally dried at 80°C for 14h to obtain lignin / calcium-based montmorillonite (the mass ratio of raw material alkali lignin and calcium-based montmorillonite is 1:1), which is set aside.
Embodiment 2
[0025] At room temperature, add 30 grams of alkali lignin, 19.5 grams of calcium-based montmorillonite, 8.4 grams of magnesium sulfate heptahydrate and 120 grams of deionized water into a 500-ml ball mill jar, mix, the pH of the mixture is 8, and ball mill for 3 hours , and finally dried at 80° C. for 16 hours to obtain lignin / calcium-based montmorillonite (the mass ratio of the raw materials alkali lignin and calcium-based montmorillonite is 1:1), which is set aside.
Embodiment 3
[0027] At room temperature, add 30 grams of alkali lignin, 19.5 grams of calcium-based montmorillonite, 9.6 grams of zinc sulfate heptahydrate and 120 grams of deionized water into a 500-milliliter ball milling tank, mix, the pH of the mixture is 7, and ball mill for 3 hours , and finally dried at 80°C for 20 hours to obtain lignin / calcium-based montmorillonite (the mass ratio of the raw material alkali lignin and calcium-based montmorillonite is 1:1), which is set aside.
PUM
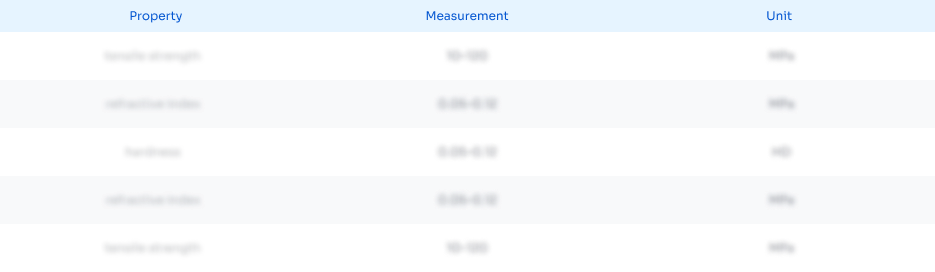
Abstract
Description
Claims
Application Information

- R&D
- Intellectual Property
- Life Sciences
- Materials
- Tech Scout
- Unparalleled Data Quality
- Higher Quality Content
- 60% Fewer Hallucinations
Browse by: Latest US Patents, China's latest patents, Technical Efficacy Thesaurus, Application Domain, Technology Topic, Popular Technical Reports.
© 2025 PatSnap. All rights reserved.Legal|Privacy policy|Modern Slavery Act Transparency Statement|Sitemap|About US| Contact US: help@patsnap.com