Apparatus and method for isolating temperature influence by using two surface acoustic wave resonators
A surface acoustic wave, temperature separation technology, applied in the direction of using ultrasonic/sonic/infrasonic waves, measuring devices, instruments, etc., can solve the problem that the SAW strain sensor cannot be used
- Summary
- Abstract
- Description
- Claims
- Application Information
AI Technical Summary
Problems solved by technology
Method used
Image
Examples
Embodiment Construction
[0017] 1. Preparation of SAW resonators: SAW resonators are manufactured on piezoelectric substrates with different tangential directions by microelectronic lithography technology, and Au electrodes are grown on the substrates by electron beam evaporation technology, and then peeled off by glue remover. The remaining glue is used to make SAW resonators, and a layer of Si0 is deposited on one of the SAW resonators by plasma chemical vapor deposition. 2 film, changing the transition temperature of this device to be the same as that of the other device, i.e.
[0018] 2. Temperature strain test: Bond the two devices prepared in step 1 to the same horizontal position on the strain test piece, and the SAW propagation direction is parallel to the main strain direction. Strain tests were performed on the two devices at different temperatures to obtain f r01 , a 1 , f r02 , a 2 ,s 1 ,s 2 and other parameter values. After obtaining these parameters, by testing the strain freque...
PUM
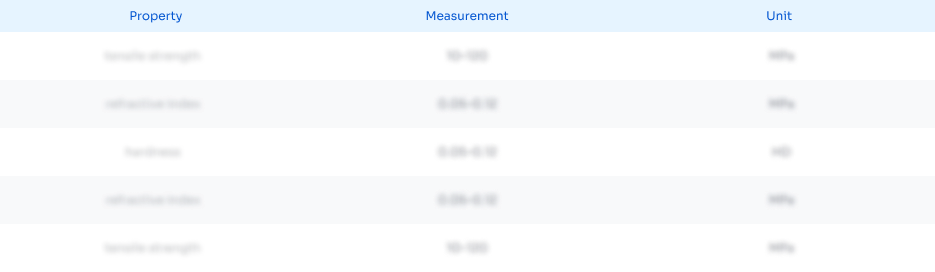
Abstract
Description
Claims
Application Information

- R&D
- Intellectual Property
- Life Sciences
- Materials
- Tech Scout
- Unparalleled Data Quality
- Higher Quality Content
- 60% Fewer Hallucinations
Browse by: Latest US Patents, China's latest patents, Technical Efficacy Thesaurus, Application Domain, Technology Topic, Popular Technical Reports.
© 2025 PatSnap. All rights reserved.Legal|Privacy policy|Modern Slavery Act Transparency Statement|Sitemap|About US| Contact US: help@patsnap.com