Breathable wearing-resistant fabric material and preparation method thereof
A technology of textile materials and raw materials, which is applied in the field of breathable and wear-resistant textile materials and their preparation, can solve problems such as sagging, lack of elasticity, and easy deformation, and achieve the effects of strong friction resistance, strong practicability, and cheap raw materials
- Summary
- Abstract
- Description
- Claims
- Application Information
AI Technical Summary
Problems solved by technology
Method used
Examples
Embodiment 1
[0029] (1) Take by weight 50 parts of apocynum fiber, 40 parts of viscose fiber, 35 parts of polylactic acid, 30 parts of trimethyl metasilicate, 20 parts of dilauryl thiodipropionate, dodecylbenzene 18 parts of sodium sulfonate, 12 parts of phosphatidylethanolamine, 8 parts of potassium metabisulfite, 6 parts of cetyltrimethylammonium bromide, 6 parts of hydroxypropyl starch, 4 parts of nano silicon dioxide, cetyl alcohol sulfuric acid 4 parts of ester sodium salt, 3 parts of linoleic acid, 2 parts of silane coupling agent KH-590, 2 parts of sulfenamide, 160 parts of deionized water;
[0030] (2) Polylactic acid, trimethyl metasilicate, dilauryl thiodipropionate, sodium dodecylbenzenesulfonate, phosphatidylethanolamine, potassium metabisulfite, cetyl trimethyl bromide Mix ammonium, hydroxypropyl starch and deionized water, place on a magnetic stirrer and stir at a speed of 650r / min for 35min, then heat up to 80°C, and bathe in water for 15min to obtain a preliminary mixture; ...
Embodiment 2
[0036] (1) Take by weight 53 parts of apocynum fiber, 45 parts of viscose fiber, 40 parts of polylactic acid, 35 parts of trimethyl metasilicate, 23 parts of dilauryl thiodipropionate, dodecylbenzene 20 parts of sodium sulfonate, 14 parts of phosphatidylethanolamine, 10 parts of potassium metabisulfite, 7 parts of cetyltrimethylammonium bromide, 7 parts of hydroxypropyl starch, 5 parts of nano silicon dioxide, cetyl alcohol sulfate 5 parts of ester sodium salt, 4 parts of linoleic acid, 3 parts of silane coupling agent KH-550, 3 parts of epoxy resin, 160 parts of deionized water;
[0037] (2) Polylactic acid, trimethyl metasilicate, dilauryl thiodipropionate, sodium dodecylbenzenesulfonate, phosphatidylethanolamine, potassium metabisulfite, cetyl trimethyl bromide Mix ammonium, hydroxypropyl starch and deionized water, place on a magnetic stirrer and stir at a speed of 700r / min for 40min, then heat up to 85°C, and bathe in water for 20min to obtain a preliminary mixture;
[0...
Embodiment 3
[0043] (1) Take by weight 55 parts of apocynum fiber, 50 parts of viscose fiber, 45 parts of polylactic acid, 40 parts of trimethyl metasilicate, 26 parts of dilauryl thiodipropionate, dodecylbenzene 22 parts of sodium sulfonate, 16 parts of phosphatidylethanolamine, 12 parts of potassium metabisulfite, 8 parts of cetyltrimethylammonium bromide, 8 parts of hydroxypropyl starch, 6 parts of nano silicon dioxide, cetyl alcohol sulfate 6 parts of ester sodium salt, 5 parts of linoleic acid, 4 parts of silane coupling agent KH-560, 4 parts of polyvinyl alcohol, 160 parts of deionized water;
[0044] (2) Polylactic acid, trimethyl metasilicate, dilauryl thiodipropionate, sodium dodecylbenzenesulfonate, phosphatidylethanolamine, potassium metabisulfite, cetyl trimethyl bromide Mix ammonium, hydroxypropyl starch and deionized water, place on a magnetic stirrer and stir at a speed of 750r / min for 45min, then heat up to 90°C, and bathe in water for 25min to obtain a preliminary mixture;...
PUM
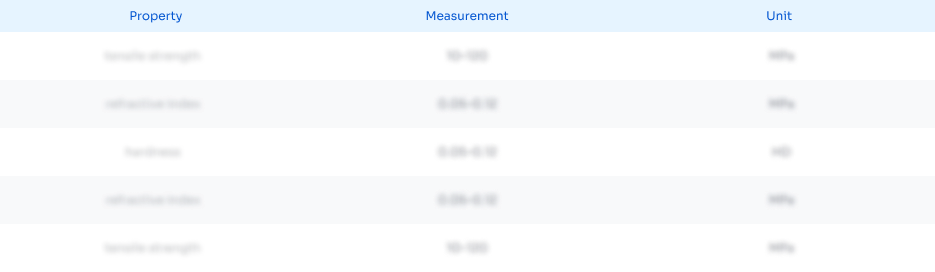
Abstract
Description
Claims
Application Information

- Generate Ideas
- Intellectual Property
- Life Sciences
- Materials
- Tech Scout
- Unparalleled Data Quality
- Higher Quality Content
- 60% Fewer Hallucinations
Browse by: Latest US Patents, China's latest patents, Technical Efficacy Thesaurus, Application Domain, Technology Topic, Popular Technical Reports.
© 2025 PatSnap. All rights reserved.Legal|Privacy policy|Modern Slavery Act Transparency Statement|Sitemap|About US| Contact US: help@patsnap.com