Servo control method for gasoline engine speed in hydraulic system of legged robot
A gasoline engine and hydraulic system technology, applied in the direction of engine control, machine/engine, electrical control, etc., can solve the problems that cannot meet the speed control of high-power engines, increase the difficulty of assembly, and complicate speed measurement, so as to reduce the difficulty of mechanical assembly and speed measurement Convenience and guaranteed speed stability
- Summary
- Abstract
- Description
- Claims
- Application Information
AI Technical Summary
Problems solved by technology
Method used
Image
Examples
Embodiment Construction
[0040] The speed servo control method of the gasoline engine of the leg-foot robot hydraulic system of the present invention adopts a speed measuring circuit such as figure 1 As shown, the method of directly using the engine ignition signal to measure the engine speed is adopted. Since the initial signal peak-to-peak value is about 100V, it needs to be controlled by R 1 and R 2 The resistor divider network formed in series is used for step-down processing, and the processed voltage U 2 =U 1 *R 2 / (R 1 +R 2); after passing through the photocoupler, the signal is converted into a DC signal by using its one-way passing characteristic; finally, after being compared with the comparison voltage by the comparator LM393, the output square wave waveform with an amplitude of 5V is captured and calculated by the microcontroller capture module Speed, the calculation formula is v fed =60*f, where f is the frequency of the square wave captured by the single chip microcomputer.
[00...
PUM
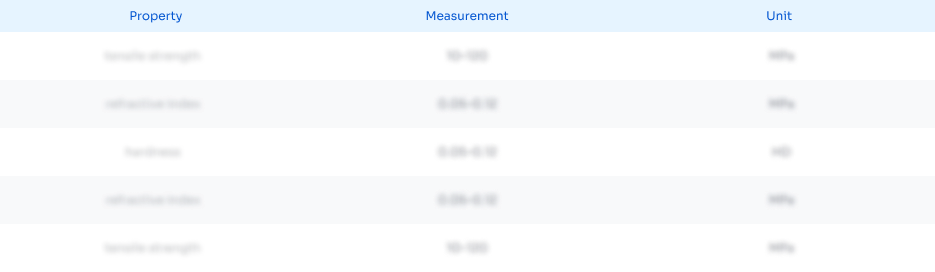
Abstract
Description
Claims
Application Information

- Generate Ideas
- Intellectual Property
- Life Sciences
- Materials
- Tech Scout
- Unparalleled Data Quality
- Higher Quality Content
- 60% Fewer Hallucinations
Browse by: Latest US Patents, China's latest patents, Technical Efficacy Thesaurus, Application Domain, Technology Topic, Popular Technical Reports.
© 2025 PatSnap. All rights reserved.Legal|Privacy policy|Modern Slavery Act Transparency Statement|Sitemap|About US| Contact US: help@patsnap.com