Hollow shaft machining method
A processing method and hollow shaft technology, applied in the direction of drilling dies for workpieces, etc., can solve the problems of low part processing qualification rate, long part processing cycle, and high part processing cost, so as to achieve low processing cost, short processing cycle, and low cost. The effect of processing costs
- Summary
- Abstract
- Description
- Claims
- Application Information
AI Technical Summary
Problems solved by technology
Method used
Image
Examples
Embodiment Construction
[0030] The embodiments of the present invention will be described in detail below with reference to the accompanying drawings, but the present invention can be implemented in many different ways defined and covered by the claims.
[0031] refer to Figure 1 to Figure 3 , the preferred embodiment of the present invention provides a hollow shaft processing method for processing a bar into a hollow shaft 10, the outer circumference of the hollow shaft 10 is provided with an annular step 101, and the hollow shaft 10 has a central through hole 102, The outer circle of the hollow shaft 10 is also provided with a plurality of vertically penetrating pin holes 103, and the hollow shaft processing method includes the following steps:
[0032] machining the bar stock to shape it into a semi-finished product 20 with a step and a central through hole 102;
[0033] Stabilize the semi-finished product 20 to release machine stress;
[0034] semi-finishing and stabilizing semi-finished produ...
PUM
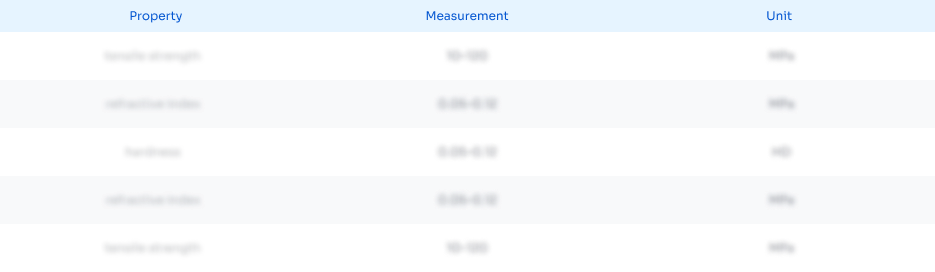
Abstract
Description
Claims
Application Information

- Generate Ideas
- Intellectual Property
- Life Sciences
- Materials
- Tech Scout
- Unparalleled Data Quality
- Higher Quality Content
- 60% Fewer Hallucinations
Browse by: Latest US Patents, China's latest patents, Technical Efficacy Thesaurus, Application Domain, Technology Topic, Popular Technical Reports.
© 2025 PatSnap. All rights reserved.Legal|Privacy policy|Modern Slavery Act Transparency Statement|Sitemap|About US| Contact US: help@patsnap.com